Das können wir für Sie tun!
Im Rahmen unseres einzigartigen und bewährten Revisions,- und Optimierungskonzepts für wassergekühlte Porsche Motoren, wurden in den letzten 20 Jahren fast 2000 erfolgreiche Motorreparaturen an Porsche 996/986/997 und 987 Motoren mit Saugrohreinspritzung der Motorgenerationen M96 und M97 durchgeführt. Nahezu allen Motoren "starben" an einem Kolbenfresser. Das Konzept wurde von uns in den frühen 2000er Jahren in Kooperation mit unserem Entwicklungspartner in Großbritannien entwickelt. Inzwischen wurden dabei fast 12.000 Kolben in die Hand genommen. Mehr als 3000 Kolben waren stark beschädigt und mussten ersetzt werden. Fast 9000 gebrauchte, teilweise leicht beschädigte Kolben, konnten aufgearbeitet und dabei in einen quasi Neuzustand versetzt werden. Dafür wurden diese akribisch gereinigt und vermessen um dann, mit der jeweiligen "State-Of-The-Art" Gleitbeschichtung auf den Kolbenhemden versehen.
Im Rahmen der Analyse der ebenfalls vermehrt auftretenden Motorschäden bei den Nachfolgemotoren der Saugrohreinspritzer, den ersten Porsche-Motoren mit Benzin-Direkteinspritzung in den Fahrzeugen der Generation Porsche 997/2 und 991 wurden wir erneut mit unterschiedlichen Schadensbildern von Kolbenfresser und sogar geschmolzenen Kolbenböden konfrontiert. Häufig waren es Kolbenklemmer, die unter ungünstigen Betriebsbedingungen, zu Fressern im unteren Bereich des Zylinders führten. Die meisten dieser Schäden waren und sind der Entscheidung des Motorenherstellers geschuldet, ein recht "enges" Kolbenspiel für diese Motoren zu wählen. Aber auch defekte Hochdruck-Einspritzventilen und/oder fehlerhaften Einspritzpumpen führten zu fatalen Motorschäden, erkennbar an thermischen Schäden an den Kolbenböden. Dass die heutigen verschärften Abgasgesetze im Rahmen der irrsinnigen CO2-Diskussion den Herstellern das Leben schwer machen, sollte dabei nicht unerwähnt bleiben. Trotz unterschiedlicher Ursachen hat man es bei beiden Porsche-Motorengenerationen mit den bekannten Schadensbildern typischer Kolbenfresser zu tun. Wir tauchten recht früh in das Thema Motorrevision ein und beschäftigten uns auf Grund der ab dem Jahr 2001 immer häufiger auftretenden Motorschäden bei den Porsche Modellen 996 intensiv mit der Analyse der Ursachen. Schritt für Schritt fanden wir heraus warum es zu den Motorschäden kam. Wie so oft, lag nicht nur ein Problem zugrunde, sondern es war das Zusammenspiel verschiedener Ursachen, die zu einen Motorschaden führten. Bereits im Jahr 2003 präsentierten wir stolz eine damals einmalige und dabei auch noch finanziell interessante Reparaturlösungen für diese Schäden, für die Porsche zu Beginn nur AT-Motoren anbieten konnte. Daraus wurden dann irgendwann Long-Block-Motoren und heute sind es Short-Block-Motoren. Wir konnten diverse konstruktive Schwachpunkte des Motors als Ursache der Schäden festmachen und fanden technische Lösungen diese zu eliminieren. Unser Ziel: Es sollte nach unserer Instandsetzung des Schadens und nach der Optimierung der Motorkonstruktion nie mehr zu einem Kolbenfresser bei diesen Motoren kommen. Und genau das, gelang uns.
Ein kurzer Einstieg
Ein Zylinder bzw. eine Laufbuchse unterliegt unterschiedlichen Beanspruchungen. Dies, basierend auf den periodisch auf sie einwirkenden Gaskräfte des Verbrennungsvorgangs.
Man beobachtet:
- Teilweise hohe Reibkräfte zwischen dem Kolben; korrekt ausgedrückt, zwischen den Flanken der Kolbenringe in Abhängigkeit der einwirkenden Tangentialkraft und der Lauffläche des Zylinder.
- Einspannkräfte, speziell bei den sogenannten Open-Deck-Motoren durch die Krafteinleitung des aufliegenden Zylinderkopfs, die zu Verzug (Welligkeit und Ovaliät) des Zylinders führen (Beispiel: Alle Porsche M96/97 Motoren)
- Genereller und nicht verhinderbarer Verzug durch sich auswirkenden Temperatur,- und Druckgradienten im und auf den Zylinderwerkstoff in Längsrichtung und entlang dem Umfang.
- Sich negativ auf die Geometrie des Zylinders auswirkende Temperaturgradienten im Übergang vom mit Wasser umspülten Zylinder zum Motorgehäuse. Hinweis: Diese entstehen meist durch ungleiche Kühlung bzw. der damit verbundenen ungleichen thermische Ausdehnung und/oder Wärmeabfuhr. Der dabei entstehende Verzug und die nicht kontrollierbaren Spannungen resultieren in Deformationen der Zylinder. Bemerkung: Dies ist der Hauptgrund für alle im UT beginnenden Kolbenfresser bei den Porsche Direkteinspritzer-Motoren der Typen MA1/XX ab dem Modell 997/2. Der untere Bereich der Zylinder führt auf Grund der "stabilen" Anbindung zum Kurbelgehäuse einen Großteil der Wärme in das Gehäuse ab. Die thermische Expansion verläuft in diesem Bereich deutlich langsamer als im oberen Zylinderbereich. Als Folge wird es dem Kolben, der sich schnell auf seinen Maximaldurchmesser ausdehnt, im Bereich des unteren Totpunkt, genau da, wo es zu einem Kippen kommt, zu eng und er frisst.
- Nicht normativer Verschleiß der Lauffläche aufgrund von Mischreibung durch Kolben und Kolbenringe (Hinweis: nicht zu vermeiden bei falscher Auslegung!)
- Nicht normativer Verschleiß. Sichtbar auf der Zylinderlaufbahn und den Kolben, speziell an riefigen Kolbenhemden, mind. aber mit partiell abgetragenen Beschichtungen auf Grund eines zu eng ausgelegten Kolbenspiels und/oder zu hohen Tangentialkräften der Kolbenringe.
- Starke Ablagerungen von Ölkohle im Bereich OT des Zylinders und am Feuersteg des Kolbens. Ursache sind zu hohe Temperaturen am Kolbenboden (>240°C), speziell oberhalb der Ringzone (Feuersteg-Bereich) in Verbindung mit einem erhöhten Eintrag von Öl in den Brennraum. Hinweis: Minimieren kann man diese hohen Temperaturen durch das Aufbringen unseres CPHC Thermo-Coatings auf den Kolbenboden und den Bereich des Feuerstegs des Kolbens.
Und was gilt es zu minimieren oder zu verhindern?
- Unterschiedlichen, auf der Zeitachse nicht harmonierenden thermischen und mechanische Verzug/Ausdehnung der in Kontakt stehenden Kolben und Zylinder. Lösung: Eine sich der Brennraumgeometrie selbst anpassende Kolbenhemdbeschichtung von Cartronic.
- Ölverkokungen: Vermeidbar sind diese nicht. Vermindern kann man diese aber, in dem man versucht die Temperatur der Kolben oberhalb der Kolbenringzone, dem Feuerstegbereich, möglichst unter 230 °C hält. (Eine sich positiv auswirkende technische Lösung: Die Cartronic-CPHC-Kolbenbodenbeschichtung mit unserem hochtemperaturfestem [>1400° C] Thermo-Coating.)
- Das Kolbenkippen im Allgemeinen. Lösung: Das Auftragen der Kolbenhemdbeschichtung von Cartronic.
- Ein zu enges und zu weites Kolbenspiel Lösung: Individuell angepasstes Stoßspiel der Kolbenringe und ein exakt bemessenes Kolbenhemdcoating von Cartronic.
- Zu hohe Temperaturen auf dem Kolbenboden Lösung: Anpassung der EInspritzmenge und turnusmäßige Wartung der EInspritzventile durch Cartronic.
- Reibung zwischen Kolbenhemd, Kolbenringflanke und Zylinderlaufbahn Lösung: Fein-Honing der Zylinderlaufbahn vor Inbetriebnahme des Motors nach Revision.
Thema: Zylinder Laufbuchsen
Bei sogenannten Laufbuchsen unterscheidet man zwischen Buchsen die im Rahmen der Produktion des Kurbelgehäuses in den Motorblock eingegossen werden und auswechselbaren Zylinderbuchsen (Losteile). Möchte man Buchsen eingießen, können die unterschiedlichsten Gehäuse,- und Zylinderwerkstoffen kombiniert werden.
Im Bereich der Motorinstandsetzung verwenden die meisten Instandsetzungsbetriebe trockene Laufbuchsen die i.d.R. eingepresst werden. (Block erwärmen, Zylinder kühlen und hinein damit). Vorher werden die beschädigten Zylinder im Block aufgebohrt um dann die passenden Büchsen einzupressen. Dabei handelt es sich um eine einfach durchzuführende und zugleich finanziell günstige Reparaturmöglichkeit. Allerdings auch um eine der im Vergleich zu anderen, meist auch den Profis unter den Motorinstandsetzungsfirmen unbekannte Möglichkeiten, technisch schlechtesten Vorgehensweisen. Das die Wärmeübergang zwischen Büchse und Zylinder/Blockmaterial sehr schlecht ist und die unterschiedlichen thermischen Ausdehnungsraten von Aluminium und Grauguss keine lange Haltbarkeit prophezeien, versteht sich von selbst.
Trockene Laufbuchse werden mit Wandstärke zwischen 2 bis 3 mm aus qualitativ mehr oder minder guten Schleudergussmaterial gefertigt. Schleuderguss-Zylinder genießen im konventionellen Instandsetzungsbereich einen guten Ruf, sind haltbar, einfach zu bearbeiten und bergen somit keine großen Überraschungen. Als Reparaturzylinder haben sie definitiv ihren Platz gefunden, da es neben speziellen anderen Zylindern aus Aluminiumlegierungen (z.B. Alusil-Büchsen für Alusil-Motoren) meist keine andere Möglichkeit gibt, einen Zylinder mit Kolbenfresser wieder herzustellen.
Wie bereits erwähnt, gießen nicht wenige Großserien-Motorenhersteller im Schleudergussverfahren produzierte Büchsen in ihre Motoren mit Aluminium-Gehäuse ein. Dies trägt zu einer Erhöhung der Formstabilität des Kurbelgehäuses bei und erlaubt die Motorkonstrukteure mit recht geringen Zylinderabständen zu arbeiten ohne dabei Stabilität einzubüßen.
Nun zu unserer Entwicklung
Cartronic hat Hybridzylinder entwickelt, die zwei Welten miteinander vereinen. Unsere Zylinder bestehen aus zwei miteinander vergossenen unterschiedlichen Materialien. Innen befindet sich ein Zylinder aus dem hochwertigsten Schleuderguss aus deutscher Produktion. Darin läuft später der Kolben. Vergossen bedeutet, dass der innere Zylindern in einer Kokille in die der Zylinder eingelegt wird, mit Aluminium umgossen, bzw. eingegossen wird. Der äußere Bereich besteht im Idealfall aus der gleichen Aluminiumlegierung wie das Motorgehäuse in der der Zylinder eingebracht werden soll. Zylinder mit diesen Eckdaten verwenden wir seit Anfang 2024 im Rahmen der Reparaturen der durch Kolbenfresser beschädigten wassergekühlten Porsche Boxster, Cayman, 996 und 997 Motoren der Typen M96 und M97. Dafür wird das Rohteil nach dem Guß und vor dem Einbau in den Motorblock entsprechend mechanisch bearbeitet. In Kombination mit der von uns entwickelten und im weiteren Verlauf beschriebenen Kolbenhemdbeschichtung sowie des Thermo-Coatings auf den Kolbenböden, ist es möglich aus einem, mit diversen konstruktiven Unzulänglichkeiten behafteten Open-Deck Porschemotor ein quasi „unkaputtbares“ Closed-Deck-Triebwerk für diese Fahrzeuge zu bauen.
Vorteile der Cartronic Hybrid-Zylinder:
- Die Materialzusammensetzung des mit dem Block in Kontakt stehenden Zylinderbereichs entspricht der des Kurbelgehäuses. Dadurch harmoniert die thermische Ausdehnung der Bauteile auf der Zeitachse. Ganz im Gegensatz zu aufgebohrten und mit dünnen sogenannten "Stahlbüchsen" versehenen Reparatur-Zylindereinsätzen (sogenannte Stahlbüchsen!)
- Verkörpern die Hauptkomponente des weltweit technisch besten Reparaturkonzepts für Porsche M96 und M97 Motoren.
- Deutlich leiserer Motorlauf im Vergleich zum Serienmotor. (Ursache: Schallschluck-Effekt durch die Kombination unterschiedlicher Werkstoffe)
- Sehr stabil. Sogar für nachträglich aufgeladene Motorkonzepte i.V.m. konstruktiv verändertem Pleuellagern geeignet.
- Sofort verfügbar ab Hersteller in Deutschland für 96mm und 99mm Bohrung.
Weitere Aussagen zu diesem speziellen, wenn auch interessanten Themenbereich würde den Umfang an dieser Stelle sprengen. Wenn Sie sich für unseren ausführlichen Erfahrungsbericht, die Analyse und die Reparaturmethode der betroffenen Porsche-Motoren interessieren, dann klicken Sie bitte auf die folgende Schaltfläche und laden Sie sich das 120-seitige Dokument "Time Over?" von unser Webseite herunter.
Link zum Cartronic Erfahrungsbericht "Time Over?"
Im Rahmen der Motorrevisionen wurden in früheren Zeiten beschädigte (gefressene) Kolben gegen neue ersetzt. Die unbeschädigten Kolben wurden gereinigt und mit neuen Kolbenringen versehen. Um leicht beschädigte Kolben weiter zu verwenden arbeiteten wir seit dem Jahr 2003 bis 2023 mit verschiedenen Dienstleister zusammen, die Gleitbeschichtungen für Kolben anboten und teilweise bis heute anbieten. Verarbeitet werden generell industriell hergestellte Gleitlacke aus den unterschiedlichsten Grundstoffen und Qualitäten. Restlos alle Anbieter versprachen viel und waren zusammen mit ihren Beschichtungen schon mindesten einmal im Weltall. Leider konnte kein Dienstleister oder Produkthersteller halten, was versprochen wurde. Besonders ein Hersteller, der seit vielen Jahren eine in der Branche hochgepriesene Dünnschicht PTFE-Beschichtung anbietet, enttäuschte uns besonders. Die ursprünglich für Bratpfannen entwickelte Beschichtung, sollte auch für Kolbenhemden funktionieren. Ja, sie funktionierte, aber auf einem Kolbenhemd im laufenden Motor, jedoch nur für einige Stunden, dann war sie abgerieben. Nicht selten hat man es bei Motorrevisionen mit leicht, im einstelligen bis kleinen zweistelligen Hundertstel Millimeterbereich durch eine Reparaturhonung vergrößerten Bohrungsdurchmesser zu tun. Um das Kolbenspiel anzupassen bedient man sich einer dicker aufgetragenen Gleitschicht auf die Kolbenhemden. Leider konnten wir kein haltbares "Dickschicht-Coating" auf dem Weltmarkt auftun. Der Bedarf an einer Beschichtung, welche es erlaubt einen Kolbendurchmesser an einen neuen Bohrungsdurchmesser nach der Bearbeitung von Zylindern mit Kolbenfressern anzupassen, ist nicht zu unterschätzen. Nach fast 17-jähriger Unzufriedenheit machten wir uns dann Mitte 2020 ernsthaft Gedanken wie eine gute Kolbenhemdbeschichtung von der Chemie her aufgebaut sein müsste und formulierten auch gleich ein Anforderungsprofil. Ohne die Hilfe von Spezialisten aus der Industrie, wäre das nicht möglich gewesen. Diese konsultierten wir im Frühjahr 2021 und begannen dann auch gleich mit der Formulierung und der Umsetzung. Das Coating sollte haltbar sein und zugleich hervorragende thermische und tribologische Eigenschaften aufweisen. Die Idee ein Dickschicht-Coating herzustellen kam erst einige Monate später auf. Diese sollte seitens der Schichtstärke eine Sicherheitsreserve (Distanz zum Kolbenmaterial) bei Motoren mit geringem Kolbenspiel bieten. Und das Ganze, trotz der Erfahrungen mit den festgestellten ungünstigen und konträr verlaufenden Ausdehnungsverhältnissen zwischen Kolben und Zylinder in den Porsche Direkteinspritzer-Motoren der Generation MA1/xx.
Technisch war es gewünscht und zudem ja auch nicht vermeidbar, dass eine Beschichtung verschleißt. Entwickelt werden sollte eine langlebige Funktionsbeschichtung die vergleichbar mit dem Verschleiß von Bremsbelägen sein sollte. Verschleißen ja, aber dabei weiterhin die Funktion (geringe Reibung / weniger Kolbenkippen usw.) gewährleisten. Wir waren der Ansicht, dass man die Beschichtung in einer Materialstärke auftragen sollte, die jede übliche gewählte Materialdicke von wenigen hundertstel Millimetern deutlich überschreitet. Wir "träumten" von einem Dickschicht-Coating welches sich von der aufgetragenen Materialdicke der Geometrie des Kolbens im Zylinder, bezogen auf die Motorbelastung anpasst. Wenig Motorbelastung = geringer Materialabtrag auf den Kolbenhemden, mittlere bis hohe Motorbelastung = mittlerer Materialabtrag des Coatings und maximale Motorbelastung = Maximal möglicher Materialabtrag des Coatings bis auf eine geringe Restdicke von 2/100mm als Sicherheitsreserve. Leider gab es eine derartig haltbare Beschichtung nicht.
Um der nicht seltenen vorkommende thermischen Ausdehnung der Kolben im Vergleich zum Zylinder auf der Zeitachse entgegen zu wirken kamen wir auf die Idee, die Kolbenböden mit einer Thermobarriere zu beschichten. Dadurch verzögert sich die thermisch begründete Ausdehnung der Kolben ein wenig. Derartige Beschichtungen waren zur der damaligen Zeit nicht wirklich etwas Neues, verfolgten aber einen anderen Sinn. Man wollte mehr thermische Energie im Brennraum halten. Wir testeten alle verfügbaren Produkte, waren bedingt begeistert und entwickelten am Endes des Tages auf Basis eines am Markt verfügbaren Spritz-Coatings eine deutlich wirkungsvollere Thermo-Beschichtung welche wir dann auch gleich auf alle Kolbenböden der von Schäden betroffenen Porsche MA1/xx Direkteinspritzer-Motoren aufbrachten. Restlos alle waren begeistert. Unser Coating zeichnet sich dadurch aus, dass es einer maximalen Temperatur von nahezu 1450°C länger widersteht als alle anderen erhältlichen Coatings. Es erfüllt daher den Zweck einer sehr effektiven Thermobarriere zwischen der Hitze des Brenngases, der Feuerstegzone und der gesamten Fläche des Kolbenbodens. Das Coating bewirkt, dass der Temperatureintrag in das Kolbenmaterial zeitlich gesehen langsamer verläuft. Nach anfänglichen Rückschlägen, sprich keinen Verbesserungen, sprachen die Erfolge dann schnell für sich. Seit dem Jahr 2023 beschichten wir alle Kolben nicht nur mit unserer CTOC-Kolbenhemdbeschichtung, sondern auch mit unserem CPHC-Thermocoating auf den Kolbenböden. Seit Herbst 2024 bieten wir alle unsere Beschichtungen auch als Servicedienstleistung, also auch für Sie an. Ab dem 4. Quartal 2025 werden wir Lizenzen für Selbstanwender vergeben. Wir hoffen, Ihr Interesse geweckt zu haben und laden Sie nun ein, mehr über unsere einzigartigen funktionalen Beschichtungen zu erfahren.
CTOC
Cartronic-Tolerance-Optimising-Coating Null-Toleranz Kolbenhemd
Beschichtung
- Haltbar + verschleißfest
- Selbsteinstellende Null-Spiel Passung
- vermindertes Kolbenkippen
- mehr Motorleistung
- weniger Laufgeräusche
- verbesserte Abgaswerte
CPHC
Cartronic-Piston-Heatschield-Coating
Hochtemperatur Coating
für Kolbenböden
- verzögerte, thermisch bedingte Kolbenausdehnung
- mehr Motorleistung
- weniger Verbrennungsrückstände
- optimierte Verbrennung
- Hitzeresistent bis 1450°C
- Rennerprobt
CPLT
Cartronic-Pistonskirt-Laserhoning-Tec
Laserhoning für Kolbenhemden
- optimierte und definierte Ölrückhaltung
- Längere Lebensdauer
- Weniger Kraftstoffverbrauch
- Kolbenindivdualisierung möglich (Logo, Seriennr.)
- Messpunktindikator auf dem Kolbenhemd möglich
CMST
Cartronic-Micro-Shotpeening-Treatment Oberflächenveredlung von hochbelasteten Motorbauteilen
- Erhöhung der Festigkeit
- Verlängerung der Lebensdauer
- Geeignet für Kurbelwellen, Nockenwellen, Kipphebel, Pleuel und Kolben
CPIP
Cartronic-Powder-Impact-Plating
Optimierung der Materialeigenschaften von
Motorbauteilen
- Erhöhung der Gefügefestigkeit
- Verbesserung der tribologischen Eigenschaften
- Auflösung von Druckspannungen im Gefüge
- Geeignet für hochbelastete Motorbauteile
CVFH
Cartronic-Vertical-Finish-Honing
Optimierung der Zylinderlaufflächen und der Kolbenringe
- Verringerung der Reibwiderstände im Zylinder
- Mehr Motorleistung
- Verkürzung der EInlaufzeit
- Verlängerung der Lebensdauer der Kolbenringe
- Senkung des Blow-By
CTOC Das Cartronic-Tolerance-Optimising-Coating
Die einzigartige Null-Passung (Zero-Clearance) Leichtlauf Gleitbeschichtung für Kolbenhemden
Beschreibung einer selbstadaptierenden, funktionalen Gleitbeschichtungen für Motor,- und Turbinenbauteilen zwecks Laufspieloptimierung und Effizienzsteigerung
Kolbenbeschichtungen sind weit verbreitet. Sie verbessern nicht nur die tribologischen Eigenschaften zwischen Kolben und Zylindern, sondern führen auch zu einer Minderung der Laufgeräusche eines Motors. Der Zweck konventioneller Beschichtungen auf Kolbenhemden besteht darin, Reibung zu verringern um den Verschleiß zu minimieren indem die Gleiteigenschaften zwischen dem an der Zylinderwandung anliegenden Kolbenhemden verbessert werden. Speziell in der initialen Einlaufphase nach erstmaliger Inbetriebnahme der Motoren macht eine Hemd-Beschichtung Sinn, denn die führt nicht nur zu einer längeren Lebensdauer des Motors bei optimierter Effizienz, sondern erlaubt sogar gewisse temporäre Notlaufeigenschaften unter extremen Betriebsbedingungen wie übermäßig hohen Temperaturen und Drücken. Kolbenhersteller verwenden meist Graphit,- oder Molybdän-Disulfid-haltige Materialien. In den letzten Jahren kamen auch Beschichtungen auf Polymerbasis zum Tragen, denen man Mos2, Graphit und/oder andere Zusätze beimischt.
Unsere Beschichtungen erfüllen selbstverständlich auch diese Anforderungen, können jedoch noch deutlich mehr. Bitte tauchen Sie tiefer in die Materie ein. Es geht neben der Minimierung von Reibung auch um die Verringerung des Verschleiß der Kolbenringe, da man durch das Auftragen unseres Kolbenhemdcoating das teilweise exzessive Kolbenkippen stark reduziert. Und es geht auch um mehr Motorleistung als Folge der Senkung der Emissionen durch Minimierung der Reibungsverluste. Wussten Sie, dass über 35% der internen Reibungsverluste aus dem Kontakt der Kolbenringe zur Zylinderlauffläche resultieren?
Merkmale verschiedener Beschichtungsmaterialien:
1. Molybdän-Disulfid (MoS₂):
Eigenschaften: MoS₂ hat ausgezeichnete trockene Schmiereigenschaften, da es einen sehr geringen Reibungskoeffizienten aufweist. Aufgetragen auf Kolbenhemden mindert es den Verschleiß zwischen Kolbenhemd und Zylinderlaufbahn.
Vorteile: Es hilft, Kaltstartbedingungen zu verbessern, bei denen der Ölfilm auf den Zylinderwänden noch nicht vollständig aufgebaut ist. Außerdem hält es hohen Temperaturen und Drücken im Motor stand.
Anwendung: Die Beschichtungen werden entweder aufgesprüht oder im Siebdruckverfahren auf Kolbenhemden aufgetragen.
2. Graphit:
Eigenschaften: Graphit verfügt ebenfalls über hervorragende tribologische Eigenschaften. Zudem ist es ein kostengünstiges Material welches häufig in der Großserie für Standardmotoren, aber auch bei einigen Kolben für Hochleistungsmotoren verwendet wird.
Vorteile: Graphit kann in sehr geringen Schichtstärken aufgetragen werden, ohne die Passgenauigkeit des Kolbens zu beeinträchtigen. Hinweis: Die vom Hersteller angegebenen Kolbendurchmesser, gemessen an den Messpunkten werden generell ohne die minimalen Schichtdicke der Beschichtung angegeben.
3. Polymere (meist in Kombination mit Festschmierstoffen wie Graphit oder MoS₂):
Polymerbeschichtungen für Kolbenhemden bestehen aus einer hochfesten Kunststoffmatrix, in welche verschiedene und allgemein bekannte Festschmierstoffen wie Graphit oder Molybdän-Disulfid (MoS₂) gegeben werden. Für Kolben von Rennmotoren greift man auf besonders leistungsfähige Spezial-Coatings zurück. In seltenen Anwendungsfällen kommen teilweise sündhafte teure Feststoff-Additiven zum Einsatz.
4. NCC-Beschichtungen (Nickel / Nickel-Phosphor Schichten)
Diese, teilweise, von der Formulierung sehr komplizierten Beschichtungen werden im industriellen Maßstab aufgebracht. Die Komposit- und Dispersionsschichten basieren primär auf Nickel als Hauptbestandteil (85-97%) und Phosphor (3-15%). Auch werden nicht selten Anteile von Chrom zugefügt. Die Schichten lassen sich sehr gut einstellen und können sowohl in galvanischen als auch chemischen Abscheideverfahren aufgebracht werden. Addiert man Siliziumcarbid (SiC) zu einer elektrolytisch abzuscheidenden Formel, nähert man sich technisch den bekannten NiSiC oder Nikasil-Beschichtungen von Zylinderlaufbahnen. Je nach Einsatzbereich können zusätzlich noch weitere Dispersionsstoffe wie PTFE und Borcarbid im Nanopartikelbereich zugefügt werden. Eine chemische Abscheidung kommt zum Tragen, wenn man Dünnschichten im Bereich 10-40µm z.B. bei Hochleistungskolben für Verbrennungsmotoren erreichen will. Dicke Schichten, z.B. für Zylinderlaufbahnen werden elektrolytisch aufgetragen. Alles in allem handelt es sich dabei um technisch ausgereifte und sehr wirkungsvolle Methoden der Oberflächenveredelung. Allerdings sind diese nicht geeignet für eine sich von der Materialschicht selbst anpassende Beschichtung von Kolbenhemden.
Eine Auswahl von weiteren reibungsminimierenden Stoffen
Polytetrafluorethylen (PTFE): Ein sehr weit verbreitetes Polymer, bekannt auch unter dem markenrechtlich geschützten Namen Teflon. Es weist zwar hervorragende Gleiteigenschaften auf, konnte sich jedoch im Bereich der Kolbenbeschichtungen trotz verbreiteter Anwendungen im Reparaturbereich bis heute keinen Namen machen. Urteil: Nicht empfehlenswert.
Polyamidimide (PAI): Hochleistungsfähige Kunststoffe, die auch bei hohen Temperaturen sehr stabil bleiben. Urteil: Kompliziert in der Formulierung, dabei aber sehr empfehlenswert.
Polyetheretherketon (PEEK): Ein weiteres Hochleistungsmaterial, das sich durch seine Temperatur- und Verschleißfestigkeit auszeichnet. Urteil: Empfehlenswert, wenn auch kompliziert in den Formulierungen.
Festschmierstoffe als Zusatz: Stoffe wie Graphit, Molybdän-Disulfid (MoS₂) und andere, teils geheim gehaltene reibungsminimierende Zusätze. Essentieller Bestandteil in verschiedenen Coatings.
Industrielle Anwender von Kolbenbeschichtungen:
FEDERAL-MOGUL/TENNECO:
Als eines der führenden Unternehmen für Automobilkomponenten, stellt der Tenneco Konzern auch beschichtete Kolben her. Die geheimen Formulierungen beinhalten Additive, wie Graphit, aber auch PTFE.
MAHLE:
Verwendet neben Polymerbeschichtungen für Kolben die in Hochleistungsmotoren verbaut werden auch Beschichtungen mit Graphitanteil, sowie im Siebdruckverfahren aufgetragene eisenhaltige Coatings. Die bekannteste MAHLE-Kolbenbeschichtung ist unter der Bezeichnung GRAFAL© bekannt, die speziell bei NIKASIL-Laufflächen zum Einsatz kommt. GRAFAL kann man ohne zu übertreiben als „Mahles Liebling“ bezeichnen. Es handelt sich um dunkelfarbene, fast schwarze Beschichtung, welche im Siebdruckverfahren auf nahezu alle Kolbenhemden aufgedruckt wird. Die Matrix dieser Beschichtung ist ein organisches Harz, in dem Graphit eingebettet wurde (GRAF steht für Graphit/Kohlenstoff). Die Beschichtung vergrößert den Durchmesser des Kolbens etwa 3-4µm (3-4/1000 mm). Dieses Aufmaß darf nicht beim Bohren bzw. finalen Honen der Zylinder berücksichtigt werden. Der Zweck der selbstschmierenden Leichtlaufbeschichtung ist, die Gleitreibung zwischen Kolben und Zylinder zu reduzieren. GRAFAL-Beschichtungen verfügen über Notlaufeigenschaften. Eine weitere von MAHLE verwendete und entwickelte Beschichtung ist die FERROPRINT Beschichtung. So sind fast alle Kolben für die Porsche M96/97, die in Lokasil-Laufflächen laufen mit FERROPRINT Pads auf den Kolbenhemden versehen. Die ersten Motoren der M96-Baureihe wurden im Boxster verbaut. Damals verzichtete man noch auf eine Beschichtung der Kolbenhemden. (Siehe Foto 1 am Ende des Texts)
Mahle bevorzugt „Grafal“ für Nikasiloberflächen und „Ferroprint“ für Alusil,- und Lokasilzylinder. Die FERROPRINT Beschichtung ist der GRAFAL Beschichtung ähnlich. Der Unterschied liegt darin, dass anstelle von Graphit in den GRAFAL-Beschichtungen, kleinste ferritische Metallfasern in die dann final eisenhaltige Matrix eingebettet werden.
KS Kolbenschmidt:
Ist einer der bekannten deutschen Hersteller von Kolben und verwendet unterschiedliche Gleitbeschichtungen auf Basis von PTFE und PAI.
Diverse Kolbenhersteller für Spezial,- und/oder Tuninganwendungen
Unzählige Kolbenhersteller, meist aus den USA setzen auf unterschiedliche Beschichtungen. Die Zusammensetzungen werden selten kommuniziert.
Fahrzeughersteller / OEM`s
Die meisten Hersteller von Sportwagen wie Porsche, Ferrari, BMW, AMG, Lamborghini verwenden in ihren Motoren Kolben mit den unterschiedlichsten Beschichtungen. Um den irrsinnigen, immer strenger werdenden Emissionsanforderungen an Verbrennungsmotoren gerecht zu werden, griffen auch Großserienhersteller von Mittelklassefahrzeugen auf Kolben mit Beschichtungen zurück. Interessant ist die Tendenz, dass man dazu übergeht, wieder Kolben ohne sichtbare Kolbenhemdbeschichtungen zu verbauen. Die Firma Porsche setzt seit einigen Jahren Kolben ohne Gleitlackbeschichtung in einigen Motorgenerationen, wie die der Direkteinspritzermotoren der Generation MA1 und anderen Saug- und Turbomotoren ein. Meist sind es vollflächige, nicht wirklich sichtbare opake NCC-Beschichtungen.
Lohnbeschichter
Weltweit betätigen sich rund 30 Lohnbeschichter mit der Aufarbeitung und Beschichtung von Kolben gem. Kundenwunsch. Dimensionen und Verwendungszweck wird diesen Firmen vorgegeben. Die verwendeten Materialien werden meist als Betriebsgeheimnis behandelt. Einige Spezialfirmen, offerieren recht leistungsfähige, wenn auch konventionelle Beschichtungen von Kolbenhemden und sogar Kolbenböden an.
Schichtstärken von Kolbenbeschichtungen
Die typischen industriell aufgetragenen Schichtstärken von z.B. Polymerbeschichtungen auf Kolbenhemden liegen im Bereich von 10 bis 15 Mikrometern (µm). Eine zu dicke Schicht kann die Toleranzen des Kolbens zum Zylinder beeinträchtigen, zu Passungsproblemen und unkontrollierten Abrieb führen. Bei der Verwendung von industriell hergestellten Produkten vermeidet man Schichtstärken von über 20 Mikrometern (µm), um eine haltbare Beschichtung zu gewährleisten.
Die von uns entwickelte, sich selbst an die Geometrien im Zylinder anpassenden Beschichtungen, werden bewusst in deutlich dickeren Stärken aufgetragen, weil sie einen anderen Zweck als nur die Verbesserung der tribologischen Eigenschaften (Reibungsminimierung) erfüllen sollen. Genau um diese Beschichtungen geht es hier. Sie eignen sich besonders für Motoren bei denen die Zylinder im Rahmen einer Schadensbehebung auf Übermaß bearbeitet wurden um damit Riefen in der Lauffläche zu beseitigen oder um leicht beschädigte Flächen an den Kolbenhemden wieder herzustellen. Von dem meist kostspieligen Erwerb von Übermaß-Kolben kann in solchen Fällen meist abgesehen werden, denn unsere Spezialbeschichtungen sind besonders flexibel und in der Lage den Schwingungen, der Krafteinleitung und auch der thermischen Ausdehnungen der Kolben zu widerstehen. Ideal wäre eine Beschichtung die sich im Laufe der Betriebszeit und damit einhergehenden Belastungen an die geometrischen Gegebenheiten im Zylinder anpasst, womit gerade ein Entwicklungsziel formuliert wurde.
Unsere neuartige CTOC-Beschichtung erfüllt diese Anforderung, denn sie passt sich in ihrer Schichtstärke durch eine gewollte Abnutzung der Schichtstärke auf den Bohrungsdurchmesser an und gewährleistet ein minimales und betriebssicheres Kolbenspiel. Dies erfolgt selektiv für jeden Zylinder. Nach Abschluss des Einlaufvorgangs ergibt sich ein großflächiges Tragbild des Kolbens im Zylinder. Diese Verteilung des Drucks des Kolbenhemds auf die Zylinderlaufbahn, verhindern punktuelle Überlastung der Kolbenhemden. Die verbesserte lineare Führung sorgt nicht nur für eine Geräuschminimierung, sondern auch für einen geringen Verschleiß der Kolbenringe, was wiederum zu einer Senkung des Schadstoffausstoß der Motoren führt.
Konventionelle Beschichtungen werden nicht zwecks einer verbesserten Abdichtung zwischen den beiden Reibpartnern (Kolbenringe und Zylinderlaufbahn) aufgetragen, sondern dafür, den partiellen Reibungskoeffizienten zwischen den Reibpartnern Kolbenhemd und Zylinderlaufbahn zu senken. Neben der Verbesserung der tribologischen Eigenschaften ergibt sich dadurch meist auch eine Minimierung der Laufgeräusche der Motoren. Beschichtungen müssen zwingend temperaturbeständig und sollten im gewissen Maß resistent gegen Verschleiß sein. Im Idealfall verhindern sie langfristig den direkten Kontakt zwischen dem Kolbenbasismaterial (meist eine Aluminiumlegierung) und der Zylinderlauffläche.
Das Kolben von den beiden Kolbenhemden bzw. der darauf aufgetragenen Beschichtung getragen werden, ist ein weitverbreiteter Irrglaube. Tatsächlich werden die Kolben von den Kolbenringen getragen die auf einem Ölfilm laufen. Die Kolbenhemden übernehmen lediglich die Aufgabe, dass die Kolben beim Wechsel der Richtung von OT Richtung UT und umgekehrt, nicht übermäßig im Zylinder kippen. Je länger die Kolbenhemden ausgebildet sind, umso weniger können die Kolben kippen. Die Kolbenringe legen sich mit einem definierten Druck an der Zylinderwandung an. Diese Kraft, die auf die Wandung wirkt, wird als Tangentialkraft bezeichnet und kann mit bestimmten Vorrichtungen gemessen werden. Der Laufwiderstand der Kolben steigt mit jeder Erhöhung der Tangentialkraft. Aber auch der Kraftstoffverbrauch. Im Rahmen der immer strenger werdenden Abgasgesetze beobachtet man, dass die Auslegungen der Kolbenringe bei modernen Motoren immer geringere Tangentialkräfte offenbaren. Auch geht man dazu über, die Kolbenringe in ihrer Höhe so gering wie möglich zu halten. Das ist technisch gesehen nicht zu beanstanden, doch erhöht das den Verschleiß der Ringe. Um diesen entgegenzuwirken kommen verschiedene Verfahren der Oberflächenbehandlung der Kolbenringe zum Einsatz. Der primäre Kolbenringverschleiß entsteht durch das zyklische Kippen der Kolben im Zylinder. Die Kolbenringe verändern dabei ihre Lage und "runden" sich an den Ecken ab (werden ballig). Leider kann man das Kolbenkippen nicht vermeiden, da man dafür ein Kolbenspiel von 0 benötigte. Übliche Kolbenspiele der "ballig" ausgeführten Kolben liegen zwischen 3 und 6/100 mm, gemessen am Kolbenhemd auf Höhe der Mittelachse der Kolbenbolzenbohrung.
Zum besseren Verständnis: Einer der beiden Kolbenhemden legt sich je nach Pleuelstellung jedem Richtungswechsel (Aufwärts/Abwärts) an die entsprechende Zylinderwandung an. Der Bereich des Kolbenhemds gleiten auf einem Ölfilm über die Lauffläche. In der Regel, bei moderater Belastung des Motors und bei noch zylindrischen und nicht bereits durch thermischen Verzug oder mechanischen Verschleiß "oval" gewordenen Bohrungen mit einer recht geringer Anpresskraft. Mit steigender Motorbelastung erhöht sich auch die Anpresskraft der Kolbenhemden während der Abwärtsbewegung nach Verbrennungsstart. Abhängig vom Pleuelwinkel wird dabei immer eine der beiden Kolbenhemdflächen stärker belastet als die andere. Ein wenig kompensieren kann man das, indem man die Bohrung für die Kolbenbolzen nicht zentrisch der Mittelachse bohrt. Dadurch verringern sich auch die Laufgeräusche des Motors. Kolben kippen generell, weil ein Kolbenspiel besteht. Die Ausführung der Kolbenringe, deren Verschleiß und der Abstand der Ringe zueinander sowie die Länge der Kolbenhemden spielen auch eine Rolle. Kippwinkel zwischen 2-3,0° sind messbar. Je stärker der Winkel umso stärker verschleißen die Kolbenringe. Mit steigender Betriebsdauer führt das nicht nur zu einem stärkeren Verschleiß der Kolbenringe und der Kolbenringnuten, sondern auch der Zylinderlaufbahnen. Entsteht dann noch eine, meist konstruktiv bedingte Ovalität der Zylinder, die man sehr oft bei Open-Deck-Motoren beobachtet, führt das zu Beginn des Prozesses zu einem Aufbrauchen der meist dünnen Kolbenhemdbeschichtung (0,75-1,2µm) und später dann zu einem Volumenverlust des Grundmaterial des Kolben und der Zylinderlaufbahn. Zu Beginn wird man einen erhöhten Ölverbrauch feststellen. Später kommt es dann zu Kolbenfressern.
High-Tech aus dem Oberbergischen Land
Wir, die Ingenieurgesellschaft Cartronic Motorsport aus Gummersbach beschäftigt sich seit über 20 Jahren mit der Revision und Optimierung von defekten Porschemotoren. Wir haben uns mit nahezu allen auf dem freien Markt erhältlichen Kolbenbeschichtungen beschäftigt und viele davon getestet. Überzeugt hat uns keine. Wirklich enttäuscht hat uns die XYLAN-Beschichtung von Whitford.
Aufgrund am Markt nicht verfügbarer langfristig haltbarer Beschichtungsmaterialien entschieden wir uns im Jahr 2020 zu einer Eigenentwicklung. Gleich zu Beginn formulierten wir das Entwicklungsziel um und erweiterten es dahingehend, eine sich in der Materialstärke selbst anpassende Kolbenhemdbeschichtung zu entwickeln. Der Sinn dahinter besteht darin, den Kolben über eine möglichst lange Betriebszeit optimal, ohne übermäßig zu kippen im Zylinder zu führen. Warum, sollte klar sein, denn reduziert man das Kippen in UT und OT, reduziert sich der Kolbenringverschleiß und der Ölverbrauch. Unser Bestreben ging in die Richtung, dass die Beschichtung nicht nur die Tribologie verbessern sollte, sondern sich auch positiv auf den Verschleiß der Kolbenringe, aber auch der Kolbenringnuten (Thema: Reibverschweißung) auswirken sollte. Wir erreichten sogar noch mehr, denn wir stellten fest, dass sich der Blow-By von Verbrennungsgasen in das Kurbelgehäuse und der Ölverbrauch der Motoren bei allen Motoren verringerte, in denen beschichtete Kolben von uns verwendet wurden. Schnell stellte sich heraus, dass wir mit unserer Beschichtung eine eierlegende Wollmilchsau geschaffen hatten.
Mit großen Entwicklungsschritten ging es weiter, denn unsere neuartigen Beschichtungsmaterialien bewährten sich nicht nur bei Kolben, sondern auch bei anderen Bauteilen in Verbrennungsmotoren wie Kompressor- und Turbinenteilen, Laufzeugen und Gehäusen von Ölpumpen, Wasserpumpen und Turboladern, von Pleuel,- und Kurbelwellenlagern sowie von Lagerzapfen auf denen Wellendichtringe (Simmerringe) laufen und allzu gerne auch einlaufen. Weiter unten Text gehen wir darauf noch im Detail ein.
Fazit: Beschichtet man Kolbenhemden mit stärkeren Schichten als in der Industrie üblich, kann man damit die Kolben-Kippwinkel auf ein Minimum und zugleich unerwünschte Kolbenbewegungen 2. Grades minimieren, optimiert dabei den Ölverbrauch und verringert den Verschleiß aller beteiligten Bauteile, besonders der Kolbenringe. Als wichtiger Faktor im Rahmen der Reduzierung des CO2 Ausstoß, verbessern sich die Emissionswerte bei einer damit einhergehenden Steigerung der Effizienz und Erhöhung der Lebensdauer der Motoren, die mit Kolben mit CTOC-Beschichtung bestückt sind.
Welche Beschichtungsmethoden sind verbreitet?
Kolbenbeschichtungen wurden früher im Lackierverfahren durchgeführt. Aus Kostengründen beschichtet man heute fast nur noch im Siebdruckverfahren. Das Siebdruck-Beschichtungsverfahren zeigt einige Vorteile gegenüber anderen bekannten Methoden. Dass Material wird exakt und ohne zeitraubende Maskierung der Kolben nur dort aufgebracht, wo es Wirkung zeigen soll. Ein weiterer Vorteil ist, dass es zu keinem Materialverlust durch das nicht zu vermeidende Overspray (Vorbeispritzen) bei Nasslackierungen kommt. Die Siebdruckbeschichtung kann problemlos in den automatisierten Fertigungsprozess integriert werden.
Auf die Eigenschaften weiterer partiell aufgebrachten OEM,- und Aftermarkt-Kolbenbeschichtungen, wie der Xylan-Beschichtungen von Whitford oder der unterschiedlichen graphithaltigen Coatings gehen wir an dieser Stelle nicht weiter ein, da keine dieser Beschichtungen signifikante Alleinstellungsmerkmale hat, sich also nicht durch bemerkenswerte Eigenschaften hervorhebt oder es sich um eine industrielle Beschichtung mit abweichenden technischen Hintergründen handelt. Allerdings halten das auf einer Polymerharz-Matrix aufgebaute, sogenannte „Eco-Tough NG/D Coating“ von Federal Mogul/TENNECO für eine interessante Entwicklung und erwähnenswert. Diese Beschichtung enthält neben dem weit verbreiteten Graphit eine zusätzliche Komponente. Man hat dem Harz, Carbon-Kurzfasern beigemischt. Diese Faserzumischung verbesserten die Stabilität der Beschichtung und und hebt sich von den recht einfach aufgebauten Coatings anderer Hersteller ab. Die Gleiteigenschaften verbessern sich dadurch nicht, dafür aber die Haltbarkeit der Beschichtung selbst. (Siehe Foto 2 am Ende des Textes)
Das CARTRONIC-Verfahren
Die von uns neu entwickelten CTOC-Beschichtungen werden nach aufwändiger mechanischer und chemischer Vorarbeit in einer Kombination aus Pulverbeschichts- und Nasslackierverfahren aufgebracht und danach unter hoher Temperatur im Ofen eingebrannt. Um die finalen Geometrien herzustellen, werden die Flächen sowohl händisch als auch mechanisch bearbeitet. Je nach Anwendungsfall erfolgt noch eine finale Flächenbearbeitung mit einem Hochleistungslaser auf die wir später noch eingehen. Die unterschiedlichen Formeln der Flüssig-Coatings setzen sich aus verschiedenen, reibungsminimierenden und dabei generell hoch wärmefesten Einzelbestandteilen zusammen und werden je nach Einsatzzweck bei uns gemäß der festgelegten Rezepte zusammengestellt, die Viskosität eingestellt und dispergiert. Ein wichtiger Bestandteil der in die chemisch recht komplizierte Polymermatrix eingebracht wird, ist ein sehr spezielles Polyamidimid in Pulverform (PAI) mit mittleren Korngrößen von 18µm. Eine weiterer, essentieller Bestandteil zeichnet sich durch seine Temperaturfestigkeit und hervorragenden tribologischen Eigenschaft aus.
Bis zum funktionierenden Coating war es ein langer Weg, denn die von uns, in Zusammenarbeit mit einigen Ingenieuren aus der Industrie ursprünglich entwickelte Formulierung, wurde bis zur Serienreife unzählige Male verändert und dabei ständig optimiert. Heute besteht die Beschichtung aus mehr als 20 Einzelbestandteilen.
Recht anspruchsvoll war die Anpassung der Formulierung, in der Hinsicht, dass diese nach dem Aufschmelzen im Laborofen, dem Abkühlen und der Bearbeitung die gewünschte Porosität aufweist. EIne Oberfläche mit einer definierten Porosität ist in der Lage als Ölrückhalte-Reservoir zu dienen. Leider waren wir nicht in der Lage den Grad der Porosität zu kontrollieren und entwickelten deshalb in Zusammenarbeit mit einem Hersteller von industriellen Hochleistungslasern ein Verfahren, um beschichtete Kolbenhemden mit Vertiefungen zu versehen, welche eine definierte Ölrückhaltung garantieren.
Alleinstellungsmerkmale unserer CTOC Beschichtung
Das Besondere unserer Beschichtung ist, dass sich das Coating während des Motorbetriebs abhängig von der Belastung des Motors an die "räumlichen" Gegebenheiten im Zylinder anpasst. Es entsteht ein gewollter Verschleiß. Dies geschieht recht exzessiv während der initialen Einlaufphase des Motors. Die aufgetragene Schicht passt sich selbstständig an die Bohrungsgeometrie jedes einzelnen Zylinders an. Eine derartig „intelligenten“ Beschichtung von Kolbenhemden, gewährleistet ein individuelles und nahezu optimales Kolbenspiel in jedem Zylinder. Das mit der Zeit entstehende, teils ausgeprägte Kippen des Kolbens im Zylinder wird auf ein Minimum reduziert. Je weniger ein Kolben kippt umso flächiger verteilt sich der Druck auf das Kolbenhemd und damit auch die Lauffläche des Zylinders. Das optimale Wirken der Kolbenringe, welches stark von der Geometrie und der Tangentialkraft beeinflusst wird, bleibt deutlich länger erhalten, da die Beschichtung einem ungleichmäßigen Verschleiß verhindert. Die Belastung auf die oberen und unteren Flächen der Kolbenringnuten sinken, was einen positiv zu bewertenden Nebeneffekt darstellt, denn dadurch mindert sich die Gefahr von partiellen Reibverschweißungen zwischen den Kolbenringflächen und den damit in Kontakt stehenden Bereichen der Kolbenringnut.
Die Anpassung der Kolbengeometrie durch den gewollten und mehr oder weniger kontrollierbaren Verschleiß der, auf die Kolbenhemden aufgetragenen CTOC-Beschichtung, erfolgt in Stufen, beginnend mit der ersten Inbetriebnahme des Motors und der damit startenden initialen Einlaufphase.
Ideal wäre, wenn sich in allen Last,- und Betriebszuständen ein maximal enges, aber dabei genügend weites Kolbenlaufspiel einstellen würde. Das ist aber nicht möglich, da sich auf Grund der dynamischen Verhältnisse (Last, Schwingungen, Drehzahl und Temperatur) und der damit einhergehenden thermischen Expansion und Verformung der Bauteile nur ein Bauteil-Spiel, bezogen auf die bis dahin erreichte, höchste mechanische und thermischen Belastung des Motors einstellen kann.
Der größte Unterschied der CTOC-Beschichtung zu anderen Anwendungen ist der, dass es sich dabei nicht nur um eine hochkomplexe Gleitbeschichtung, sondern um eine Multifunktionsbeschichtung handelt, die über gute Notlauf-, bei exzellenten Gleiteigenschaften verfügt und sich während des Betriebs des Motors auf eine quasi „Zero-Clearance“ Passung zwischen Kolbenhemd und Zylinder adaptiert.
Die Anforderungen an unsere CTOC-Beschichtung sind hoch. Gemäß unserem Anforderungsprofil muss sie sich nicht nur im gewissen Maße bei gleichzeitiger Flexibilität komprimieren lassen, also druckstabil und dabei thermisch resistent sein, sondern auch ein erstklassiges Ölrückhalteverhalten aufweisen. Das erreichten wir durch das bereits erwähnte Einbringen von thermoplastischen Pulverpartikeln, die bei hohen Temperaturen aufschmelzen und „einbrennen“. Um dem Coating die gewünschten Eigenschaften zu verleihen, werden in die Matrix speziellen Feststoffe hinzugegeben, die zum einen reibungsminimierenden sind und die Druckstabilität der Formulierungen erhöhen. Nach der händischen und mechanischen Endbearbeitung, bei der die Dimensionen wie der Durchmesser und die Balligkeit der Kolbengeometrien eingestellt und angepasst werden, erfolgt, wie bereits erwähnt je nach Anwendungsfall eine abschließende Laser-Honung der Beschichtung. Dieses Verfahren wurde von Cartronic entwickelt und ist bis heute weltweit einzigartig.
Der Vorteil im Ernstfall
Unsere CTOC-Beschichtungen schaffen eine zeitliche Sicherheitsreserve bis es nach einem eventuellen Schmierfilmabriss zu einem Kolbenfresser kommt.
Gibt es genügend Erfahrungswerte?
Cartronic ist Vorreiter dieser Technologie und nutzt das selbst entwickelte Beschichtungsverfahren im Rahmen der gut dokumentierten Reparatur,- Optimierung,- und Revisionsmethode ("Time-Over?") der mit multiplen Problemen behafteten Porsche M96/97 Motoren der Baureihen 986 / 987 / 996 / 997. Seit einigen Jahren kommen die Beschichtungen auch auch im Rahmen der Reparaturen der Porsche Benzindirekteinspritzer-Motoren der Generation MA1 zum Einsatz. Die CTOC-Beschichtung, sowie die weiter hinten beschriebene CPHC Thermo-Barrier-Beschichtungen, werden von uns auch regelmäßig auch bei Motorrevisionen aller klassischen luftgekühlten Porsche 356 und 911 Modelle eingesetzt.
Ein Alleinstellungsmerkmal der Anwendung ist, dass man durch die Beschichtung, die als reibungsminimierende und sich selbstanpassende Trennschicht zwischen Kolbenhemd Zylinderlaufbahn fungiert, optimale Bauteiltoleranzen zwischen den beiden Reibpartnern schafft, indem sich die Geometrien der Kolben über den gewünschten Verschleiß der aufgetragenen Beschichtung an die der Zylinder anpassen. Ohne eine Beschichtung und bei zu engem Kolbenspiel käme es zu einem Metall-auf-Metall-Kontakt, also wahrscheinlich zu Kolbenfressern. Motorenbauer wissen, dass je geringer das Kolbenspiel in Verbrennungsmotoren gewählt wird, umso geringer der sogenannte Blow-By von Verbrennungsgasen und Luft/Kraftstoffgemisch in das Kurbelgehäuse ist. Kolben die mit einem kleinen Einbauspiel im Zylinder laufen, neigen weniger zum Kippen, als Kolben mit einem großzügig bemessenen Einbauspiel. Enge Toleranzen erhöhen die Effizienz der Kolbenringe und damit auch den Wirkungsgrad des Motors da sich die Kolbenringe für lange Zeit in der gewünschten Geometrie befinden. Seit Mitte der 1990er-Jahre stellt man fest, dass Hersteller das Risiko eines frühen Kolbenfressers zugunsten von besseren Abgaswerten in Kauf nehmen, denn es finden dadurch messbare Verbesserungen der Abgasemissionen statt. Verschlechterungen der Abgaswerte im Laufe des Betriebs eines Motors kann man dadurch zwar nicht verhindern, werden aber durch dieses gefährliche Spiel zu Lasten der Haltbarkeit entgegengewirkt bzw. hinausgezögert.
Um beides zu erreichen, eine gute Abdichtung zwischen Kolben und Zylinder sowie eine langes Motorleben mit geringem Ölverbrauch und ohne Kolbenfresser, bietet sich die Verwendung unserer CTOC-Kolbenbeschichtung geradezu an. Diese funktioniert nicht nur in einem sehr breiten Temperatur-, und Druckbereich, sondern je nach Formulierung sowohl in geschmierten als auch in trocken laufenden Einsatzbereichen.
Mit dem auftragen des Coatings, welches sich unter Druck und Reibung jeweils nur soweit abnutzt (ein/abschleift) wie der Motor belastet wird, ergibt sich ein sogenanntes Zero-Clearance-Laufspiel bezogen auf die jeweilige Höchstbelastung des Motors. Dies galt lange Zeit als technisch nicht darstellbar. Die Materialstärke der Beschichtung wird im Idealfall so gewählt, dass eine geringe Restbeschichtung auf dem Kolbenhemd verbleibt, welche im Notfall, z.B. bei Kühlwasserverlust eine gewisse Sicherheit vor einem Kolbenfresser bietet. Nach Abschluss der stufenweise durchgeführten Einlaufphase ist die Beschichtung theoretisch ein Motorleben lang haltbar, da es im Normalfall zu keinem weiteren Volumenverlust mehr kommt.
Erfahrung aus der Praxis?
Vergleichsmessungen und Inaugenscheinnahmen von Schichtstärken auf Kolben von Rennmotoren, die regelmäßig nach einigen Einsätzen inspiziert und nicht selten vollständig zerlegt werden, zeigten, dass es zu der gewünschten Anpassung der Schicht kam, aber zu keinen abnormen Veränderungen der Oberfläche. Blanke Stellen auf den Kolbenhemden wurden nur sehr selten beobachtet. Zu Schichtablösungen wie bei einigen OEM-Beschichtungen üblich, kam es nie.
Halten wir fest: Unsere einzigartigen, toleranzoptimierenden Beschichtungen, passen sich durch gewollte und kontrollierbare Einlaufprozesse auf die maximale Minimaltoleranz unter maximalen Belastungen der Motoren an. Ein weiterer Verschleiß kann danach nur noch in einem sehr geringen Maße stattfinden und drückt sich ausschließlich in einen weiteren partiellen Volumenverlust der Beschichtung aus.
Gesetzt dem Fall es käme zu einem Eintrag von Fremdpartikel in das Motoröl, entweder durch einen Lagerschaden und/oder über die Einlasskanäle des Motors, starten generell abrasive Vorgänge im Motor. Unsere Beschichtung verfügt über deutlich bessere Notlaufeigenschaften als konventionelle Beschichtungen, da sie in der Lage ist, metallische Mikropartikel in ihrer Matrix einzubetten. Diese zeigen sich erstmalig bei zerlegten Motoren mit Lagerschäden in Mikro-Flitter die sich in der Oberfläche der Beschichtung befanden. Minimale Laufspuren in/auf den Zylinderlaufbahnen konnten in fast allen Fällen durch erneutes konventionelles maschinelles Plateauhonen oder im Rahmen unseres "Vertical-Finish-Honing" (CVFH) beseitigt werden. Diese rein händische Bearbeitung erfolgt als letzter Arbeitsgang der maschinelle gehonten Zylinderflächen. Wir führen diesen Arbeitsgang generell vor den Montage der Kolben durch. Auch verbessern wir die Kontaktflächen der Kolbenringe indem wir diese einer Feinpolitur unterziehen. Durch diese Arbeitsgänge senkt man nicht nur die Reibverluste in den Bohrungen signifikant sondern verkürzt auch die Einfahrzeit in der sich die Kolbenringen an die Geometrie der Laufbahn anpassen erheblich. Mehr dazu weiter unten im Text.
Zum besseren Verständnis: Die auf die Bauteile aufgetragene CTOC-Beschichtung fungiert in der Einlaufphase nicht nur gewollt als Opferschicht, sondern erfüllt auch den Zweck, einen geringen Anteil an mikroskopisch kleinen Fremdpartikel aufzunehmen ohne dass diese einen merklichen Verschleiß an der Zylinderlauffläche generiert.
Weitere Vorteile der CTOC-Beschichtung
Das Ölrückhaltevolumen der CTOC-Beschichtung ist zum einen aufgrund der Porosität der aufgeschmolzenen PAI-Bestandteile und zum anderen durch eine, im weiteren Verlauf beschriebene neuartige und einzigartigen Laser-Honung erstklassig. Kolbenbeschichtungen, die der Ölrückhaltung dienen waren in der Vergangenheit unbekannt. Alle bekannten Kolbenhersteller behelfen sich damit, indem sie vertikal verlaufende Drehspuren auf den Kolbenhemden erzeugen. Dies erreicht man durch die Einstellung eines höheren Vorschubs während der mechanischen Bearbeitung auf den CNC-Bearbeitungszentren. Unsere einzigartige Beschichtung in Verbindung mit der Laserhonung löst dieses Problem auf intelligente Weise und ist zudem weltweit einzigartig.
Die Cartronic CTOC-Beschichtung verlängert zwar die Lebensdauer der Kolbenringe, kann aber nicht die mit der Zeit entstehende ballige Abnutzung der Kolbenringflanken völlig verhindern. Da die Kolben aber bei geringerem Kippwinkel besser im Zylinder geführt werden, sinkt auch die partiell eingeleitete Kraft der Kolbenringflächen auf die Ober,- und Unterseiten der Ringnuten. Das Risiko von nicht gewollten Reibverschweißungen, gegen die man gem. dem Stand der Technik, mit dem Auftragen einer galvanischen Harteloxalschicht in den Ringnuten vorgeht, wird dadurch minimiert. Zusätzlich zu der Kolbenhemdbeschichtung behandelt Cartronic die Ringnuten mit einem neu entwickelten Oberflächenveredelungsverfahren. Dabei werden die Oberflächen der Ringnuten, die mit den Kolbenringen in Kontakt stehen mechanisch verdichtet und zudem werden verschleißhemmenden Materialien in die Oberfläche eingelagert. Weiter unten erfahren Sie mehr über dieses Verfahren.
Halten wir an dieser Stelle fest:
Die Beschichtung verringert das Kolbenkippen um bis zu 80%, da sich die Kolben, bedingt durch die bessere lineare Führung, nahezu optimal im Zylinder bewegen. Das führt dazu, dass die Kolbenringe für lange Zeit ihre ursprüngliche Geometrie behalten. Genau diese langfristig, nahezu perfekt gehaltene Geometrie der Kolbenringe ist, trägt wesentlich zu der Minimierung der Emissionen der Motoren bei, die mit einer CTOC-Kolbenbeschichtung versehen wurden. Warum? Zum einen bleiben die Kolbenringe über eine sehr lange Laufzeit in ihrer idealen Form und zum anderen wird der Blow-By von Verbrennungsgasen in das Kurbelgehäuse signifikant minimiert, denn mit Kraftstoff angereicherte Frisch- und Verbrennungsgase gehören nicht in das Kurbelgehäuse da diese zu einer Kontamination des Schmieröls führen. Kraftstoff im Motoröl führt auch zu einer gefährlichen Ölverdünnung, was im Extremfall zu einem Schmierfilmabriss führen kann. Der meiste Kraftstoff gelangt während der „fetten“ Kaltstart- und Warmlaufphase in das Motoröl, da in dieser Phase deutlich mehr Kraftstoff eingespritzt wird.
Einschränkungen der CTOC-Anwendung
Möchte man die werksseitige, in ihrer Stärke meist sehr dünn aufgetragene Kolbenhemdbeschichtung durch unsere CTOC-Beschichtung ersetzen kann man das tun. Allerdings erreicht man damit nur im eingeschränkten Maße die beschriebenen Vorteile. Man muss umdenken, da übliche Kolbenhemdbeschichtung einen anderen Zweck erfüllen. In den letzten Jahren werden von den Fahrzeugherstellern immer mehr Motoren mit Kolben ohne eine sichtbare Beschichtung auf den Kolbenhemden verbaut. Viele Hersteller beschränken sich auf das Aufbringen eine Nickel-Phosphat-Schicht auf ihren Kolben. Möchte man Kolben nachträglich für originale Bohrungen in Serienmotoren beschichten, gehen wir wie folgt vor: Zuerst werden die vorhandenen Beschichtungen entfernt, die Oberflächen vorbereitet und dann unsere CTOC-Beschichtung aufgetragen. In diesen Fällen aber so dick, dass man ein minimales Einbauspiel von rund 1,5-2/100mm erreicht. Im Laufe der Betriebszeit erhöht sich dies je nach erreichter Belastung des Motors.
Optimale Ergebnisse erzielt man dagegen bei gebrauchten und/oder nach einem Motorschaden überholten Motoren, bei denen die Zylinderbohrungen im Rahmen einer Schadensbehebung vergrößert wurden. Bei den Porsche Motoren, die in unserem Hause repariert werden, bauen wir generell 6 neue Zylinder ein. Die Zylinder haben eine im Vergleich zur Serie eine um 1/100mm vergrößerte Bohrung. Das vorgeschriebene Kolbenspiel von 5,5/100 (ohne die vom Hersteller aufgebrachte Hemdbeschichtung) verringern wir auf 2,5/100 (mit der Beschichtung gemessen) durch das Auftragen unserer Beschichtung. Kontrollieren lässt sich die gewünschte Funktion der Schichten auch. Solange sich nach einer starken Belastung des Motors noch eine nicht aufgebrauchte Opferschicht auf den Kolbenhemden befindet, bestätigt das, dass die Berechnung der Schichtstärke in Verbindung mit der Festlegung des Bohrungsdurchmessers korrekt war. An dieser Stelle muss bemerkt werden, dass die korrekte Festlegung der Bohrung und/oder der Dicke des Materialauftrages ohne eine entsprechende Erfahrung einem Glücksspiel nahekommt. Gerne beraten wir Sie.
Mehr zum Blow-By
Kommen wir noch einmal zurück auf die Blow-By Gase. Diese bestehen in ihrer Zusammensetzung aus einem Mix aus Abgasen, Öl, nicht verbrannten Kraftstoffen, Sauerstoff, Stickstoff, Wasser und sind generell mit Mikropartikeln kontaminiert. Der Blow-By wirkt sich sowohl im Verdichtungstakt als auch im Verbrennungstakt des Motors aus. Verhindern kann man den Blow-By nicht. Sie werden bei jedem Verbrennungsmotoren zwischen Kolben und Zylinderlauffläche vorbei, ins Kurbelgehäuse gepresst. Selbst bei sehr guter Abdichtung durch die Kolbenringe macht das Volumen dieser Gase 0,5 bis 2 Prozent des Gesamt-Gasvolumens aus. Blow-By-Gase sind zudem schädlich für die Umwelt.
Ohne eine Rückführung in den Verbrennungsablauf über das Abgasrückführungssystem würden diese Gase bis zu 50 Prozent der Gesamt-Kohlenwasserstoffemissionen eines Verbrennungsmotors ausmachen. Blow-By Gase werden über eine sogenannte Kurbelgehäuseentlüftung über einen Ölabscheider (Kondensator) durch Schläuche zurück in den Ansaugtakt des Motors geleitet, um sie von dort einer erneuten Verbrennung zuzuführen. Dieses Prinzip reduziert zwar die Emission eines Motors, doch leider auf Kosten der Lebensdauer der Motoren.
Da eine professionell aufgetragene CTOC-Beschichtung der Kolbenhemden in einer maximal stabilen linearen Bewegung des Kolbens im Zylinder resultiert und dabei das zyklische Kolbenkippen jeweils im oberen und unteren Totpunkt (OT und UT) weitestgehend verhindert, führt dies zu einer erfreulichen Reduzierung des Blow-By zwischen 70-80%. Diese signifikante Senkung geht zudem mit einer Senkung der Öltemperatur um rund 6-8% und der Wassertemperatur um 3-5% einher. Weniger heiße Gase im Kurbelgehäuse verlängern zudem die Lebensdauer der Motoren. Da die Fahrzeughersteller an einer Reduzierung der Emissionen ihrer Fahrzeuge interessiert sind, darf man davon ausgehen, dass in Zukunft viele Kolben mit einer CTOC-Beschichtung ausgeliefert werden, da unsere Technologie ohne Mehrkosten von den Herstellern in die Motorenproduktion von Verbrennungsmotoren implementiert werden kann. (siehe Grafik am Ende des Textes).
Weitere Anwendungen: Optimierungen von Turboladern, Kompressoren, Gleitlagern, Öl-, und Wasserpumpen
Nahezu alle, von Cartronic entwickelten Beschichtungs-Formeln sind darauf ausgelegt, die tribologischen Eigenschaften zu verbessern, die Lebensdauer der Motoren zu verlängern und sollen das Kolbenkippen reduzieren. Einige Spezial-Coatings wurden speziell dafür entwickelt, dass sich während des Motorbetriebs eine Zero-Clearance Laufpassung (Null-Passung) in Ölpumpen, Wasserpumpen, Verdichter-Gehäusen von Turboladern und Kompressoren einstellt. Mit Tribologie hat das nur etwas am Rande zu tun. Durch die Verringerung von Laufspielen sich drehender Bauteile verringert man die Pumpverluste auf ein Maximum. Dabei wird nicht nur die Effizienz der einzelnen Bauteile gesteigert, sondern die, des gesamten Triebwerks.
Beginnend mit der Beschichtung von Kolben, stellten wir schnell fest, dass sich unsere Beschichtungen auch für andere Motorkomponenten eignet. Bereits im ersten Jahr der Entwicklung beschichteten wir Wasser- und Ölpumpen für Porschemotoren. Später kamen Bauteile aus dem Ventil-, und Kurbeltrieb hinzu. Dass sich unsere CTOC-Beschichtungen hervorragend dafür eignen, Zero-Clearance Zustände in Turboladern zu erzeugen, also die Toleranz zwischen dem Verdichterrad, den Radien des Gehäuses und der Endplatte gegen Null zu senken, ergab sich erst im späteren Verlauf der Entwicklung. Wir stellten fest, dass sich die Effizienz eines Turboladers oder Kompressors durch unsere Beschichtung deutlich verbesserte. Bei aufgeladenen Motoren führt das nicht nur zu einer Verbesserung des Ansprechverhaltens, sondern resultiert auch immer in einer Leistungssteigerung. Mehr Füllung = mehr Leistung. Selbstverständlich lassen sich auch Laufzeuge und Gehäuseflächen in Schraubenkompressoren beschichten. Jeder, der sich mit dem Aufbau von Turboladern für den Motorsport beschäftigt, sollte Lizenznehmer von uns werden.
Eine andere Formel mit angepassten Feststoffanteil eignet sich besonders als Dünnbeschichtung auf schwimmend gelagerten Wellenzapfen. Diese laufen nicht in Lagerhalbschalen, sondern mit sehr geringen Toleranzen direkt in Gehäusebohrungen. Im Rahmen der Motorrevisionen von Porschemotoren der Baureihen M96 und M97 beschichten wir regelmäßig den Lagerzapfen der Zwischenwellen sowie alle beweglichen Teile in der Ölpumpe als auch die inneren Flächen der Gehäuse.
Unsere Beschichtung ermöglichen sogar die geometrische Wiederherstellung von durch Fremdpartikel beschädigten Flächen in Ölpumpen. Umlaufende, schmale Einlaufspuren durch Fremdpartikel im Öl und sogar mittelschwere Fressspuren mit geringer Tiefe in den Aluminiumgehäusen bedeuten ab sofort nicht mehr, dass die Pumpen zwingend ersetzt werden müssen, da man die oberflächigen Schäden durch das Aufbringen einer CTOC-Funktionsschicht wiederherstellen kann. Die sich ergebende Zero-Clearance-Toleranz zwischen den sich drehenden Teilen und den Gehäusen ist ein erfreulicher Nebeneffekt und stellt sich innerhalb sehr kurzer Betriebszeit auf ein. Da dieses geringer ist als bei einem Neuteil, macht es bei jedem Hochleistungsmotor Sinn, die Maßnahmen im Rahmen des Motorenbaus durchzuführen. Dass bedeutet, dass es möglich ist, die Effizienz sowohl einer neuen als auch einer aufgearbeiteten Ölpumpe durch eine CTOC-Schicht auf ihr technisch mögliches Maximum zu steigern. Der Erfolg der Maßnahmen zeigen sich sofort nach der Inbetriebnahme des Motors in einem ablesbar höheren Öldruck in allen Betriebszuständen.
Eine ganz besondere und einzigartige Anwendung, die nur wenigen Motorentechnikern bekannt ist, stellt das Auftragen einer speziellen Formulierung unsere CTOC-Beschichtung auf Wellenzapfen dar, die durch Wellendichtringe (Simmerringe) abgedichtet werden. Die sichere Abdichtung von bereits durch die Dichtlippen eingelaufenen Kurbelwellenzapfen, stellen einen der häufigsten und zugleich sinnvollsten Anwendungsfälle dar. Allgemein bekannt ist, dass es unmöglich ist im Rahmen eines Austauschs eines Wellendichtrings exakt die Position zu finden auf der die Dichtlippe des ursprünglich verbauten Wellendichtrings gelaufen ist. Baut man den neuen Ring auch nur leicht schräg versetzt zur alten Position ein, hat man sich dadurch eine „Ölpumpe“ in den Motor eingebaut, die Öl vom Inneren nach Außen befördert.
Beschichtet man Wellenzapfen mit einer dünnen CTOC-Schicht läuft die Dichtlippe des Wellendichtrings anfangs vollständig auf der Oberfläche dieser Schicht. Im Laufe der Einlaufphase bettet sich die Dichtlippe in die Beschichtung ein, bis sich ein perfektes Tragbild mit allerbesten Abdichtungseigenschaften gebildet hat. Dabei sollte man auf eine exakte Ausrichtung des Wellendichtrings achten. Im Idealfall dichtet nicht nur die Spitze der Dichtlippe die den Wellenzapfen berührt ab, sondern eine seitlich etwas größere Fläche, die in der Beschichtung läuft. Es entsteht ein Labyrinth. Ein weiterer immenser Vorteil: Nach der abgeschlossenen Einlaufphase, liegt der tragende Bereich der Dichtringlippe mit einer deutlich geringeren Flächenpressung (pro mm²) auf der Welle auf. Messungen haben ergeben, dass sich die wirksame Dichtfläche um zirka 300% vergrößert. Die Lebensdauer beider Reibpartner verlängert sich zudem deutlich. Ein weiterer Vorteil: Durch das Auftragen einer CTOC-Beschichtung auf einen bereits eingelaufenen Wellenzapfen, reduziert man das Risiko einer späteren Undichtigkeit signifikant. Was sagt das jedem Motorenbauer?
Seit dem Jahr 2024 führen wir auch Spezialbeschichtungen von Pleuel,- Zwischen,- und Kurbelwellenlagerschalen sowie Wellenzapfen im Dünnschichtverfahren mit einer speziell dafür entwickelten Werkstoff-Formel durch.
Halten wir fest: Die Beschichtung von Wellenzapfen, auf denen die Lippen von Wellendichtringen tragen, empfiehlt sich besonders dann, wenn es auf Grund einer langen Betriebsdauer zu einem messbaren Verschleiß an der Tragstelle des Wellendichtrings gekommen ist. Je länger die Dichtlippe eines Simmerings auf einem Wellenzapfen läuft umso tiefer arbeitet sich die Lippe ein. Im Laufe der Zeit entsteht dabei eine fühlbare Rille in der Lauffläche des Zapfens. Solange der Simmerring genau in dieser Spur läuft, kommt es über eine langen Zeitraum zu keinem Ölverlust. Installiert man irgendwann einen neuen Wellendichtring, ist es sehr wahrscheinlich, dass man diesen leicht quer zu der Einlaufspur auf dem Zapfen montiert. Die Welle wird trotz des neuen Simmerrings an dieser Stelle Motoröl verlieren. Vermeiden kann man das durch das Auftragen einer vollflächige Beschichtung mit dem von uns für diese Zwecke entwickelten Seal-Coating (Dicht-Coating) auf den Wellenzapfen. Diese Beschichtung füllt nicht nur vorhandene Einlaufspuren der Dichtlippen auf der Welle auf. sondern bietet dem Wellendichtring eine neue Oberfläche in die er einlaufen kann, denn die Dichtlippe läuft nur zu Beginn auf der Beschichtung, generiert aber schnell eine neue Einlaufspur, die für eine perfekte Abdichtung sorgt. (siehe Foto 4 am Ende des Textes)
Zusammenfassung aller Vorteile der Technologie:
- Unsere toleranzoptimierenden Gleitbeschichtungen (CTOC) auf den Kolbenhemden erhöhen die Motorleistung da das Blow-By von Abgasen reduziert wird. Dies, weil das konstruktionsbedingte „Kippen“ der Kolben nach dem oberen Totpunkt (OT) auf dem Weg nach unten und nach dem unteren Totpunkt (UT) auf dem Weg nach oben, auf ein Minimum reduziert wird.
- Die Kolbenringe nutzen sich gleichmäßig und weitestgehend nicht mehr ballig, sondern „rechtwinklig“ ab.
- Die Lebensdauer von Kolben/Zylinderpaarungen aber auch anderen Bauteilen, bei denen es auf eine Passung mit geringen Laufspielen ankommt, wird verlängert.
- CTOC-Beschichtungen erhöhen den Wirkungsgrad von Turboladern und Kompressoren, sowie von Öl- und Wasserpumpen, da sich Spaltmaße auf ein absolutes Minimum einstellen.
- Kolben, die mit dem CTOC-Coating beschichtet wurden, führen zu einer Verbesserung der Abgasemissionen des Motors.
- Die Beschichtung erlaubt einen Verzicht auf kostenintensiven Bauteilbearbeitungen und führt daher zu Kostenersparnissen.
- Auf konventionelle Kolbenhemdbeschichtungen sollte zu Gunsten einer CTOC-Beschichtung von Cartronic verzichtet werden.
- Die CTOC-Beschichtung ist mit sehr geringen Mehrkosten realisierbar.
Preisliste Stand 1.Mai 2025
Hier unsere Preisliste für die Beschichtung von Kolbenhemden und Kolbenböden. Wir gehen von der Anlieferung von grob gereinigten Kolben aus. Öle, Fette sollten entfernt sein.
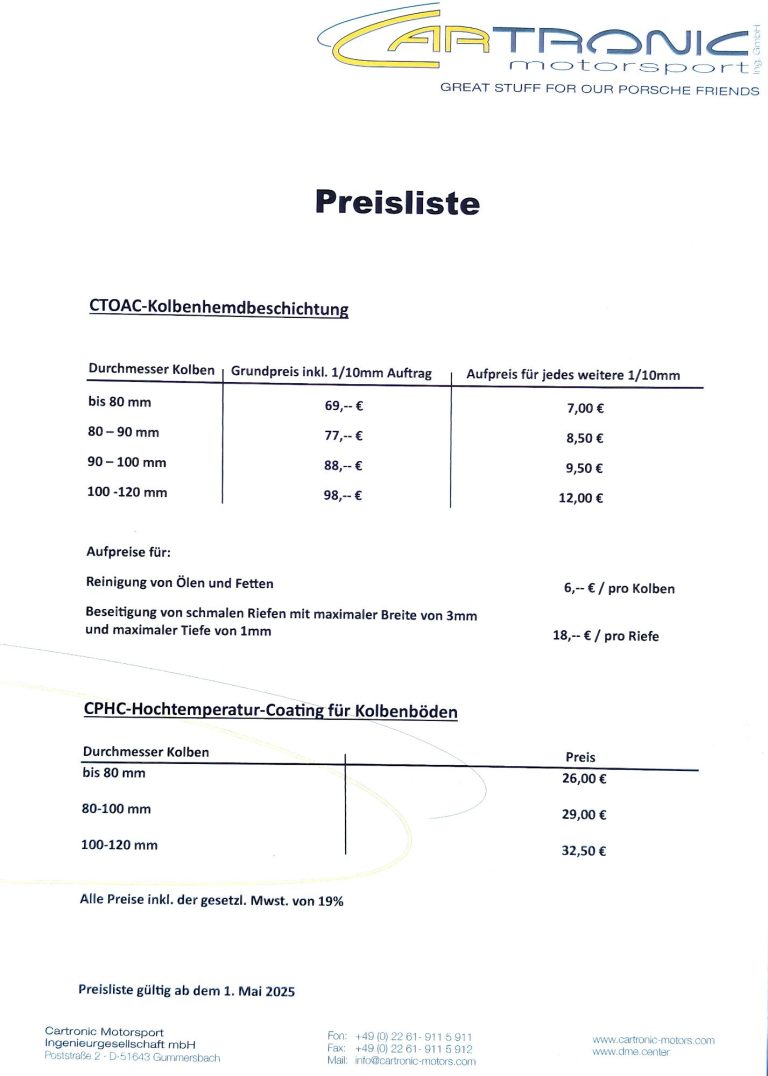
Im Detail
Die Fotos und Grafiken helfen Ihnen, mehr Verständnis zu erlangen.
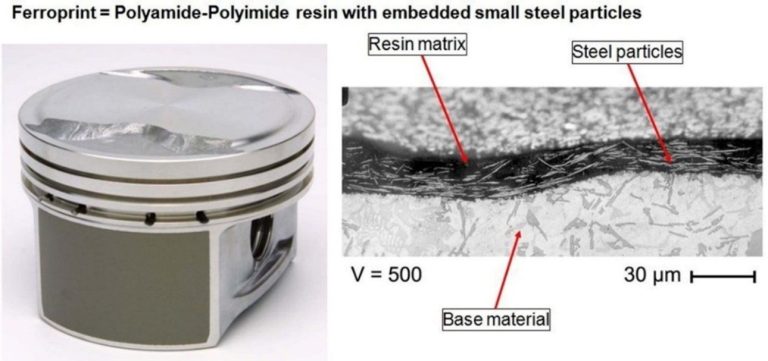
Foto 1: Ferroprint-Coating Copyright: Mahle AG
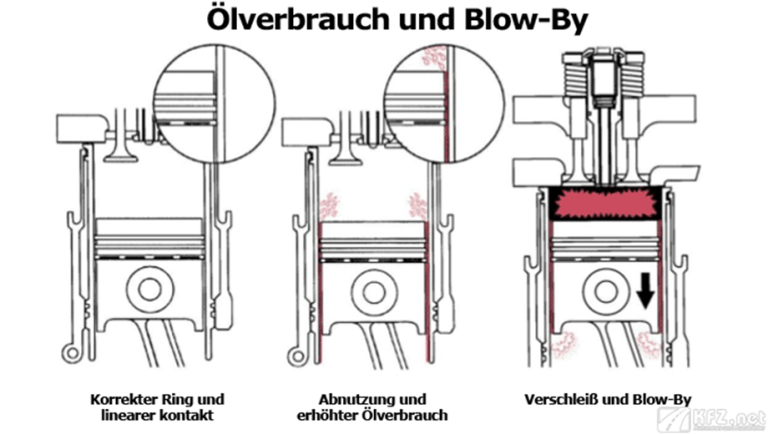
Darstellung 3: Typische Ursachen von erhöhten Ölverbrauch und Entstehung von Blow-By in das Kurbelgehäuse / Quelle: kfz.net
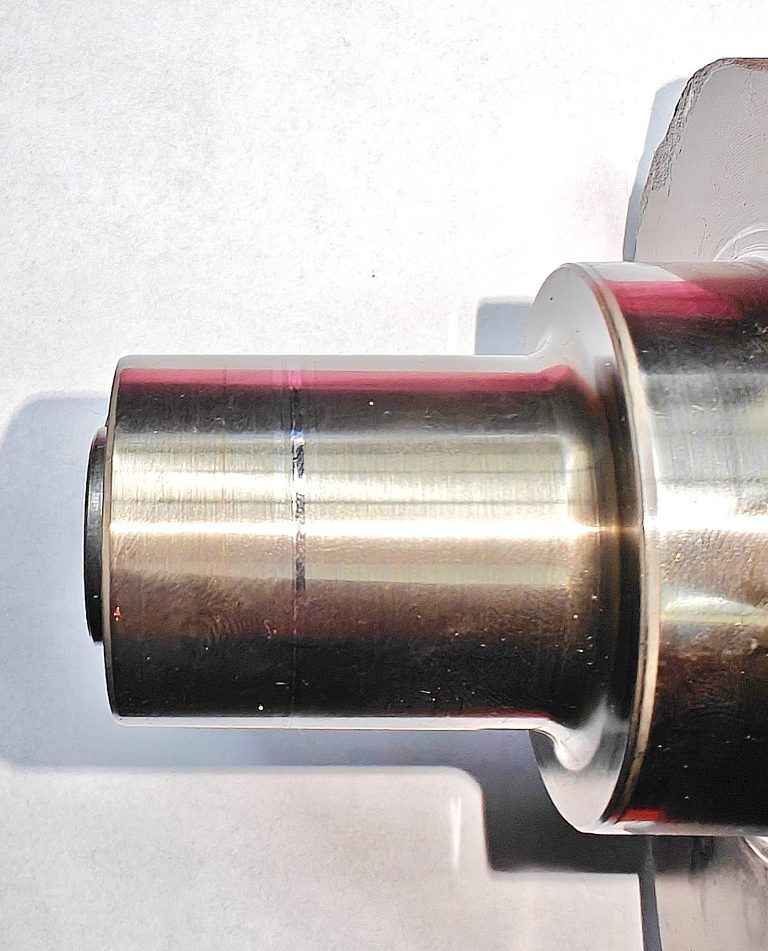
Foto 4: Lagerzapfen einer Kurbelwelle mit deutlich sicht-, und fühlbarer Einlaufspur vom Wellendichtring
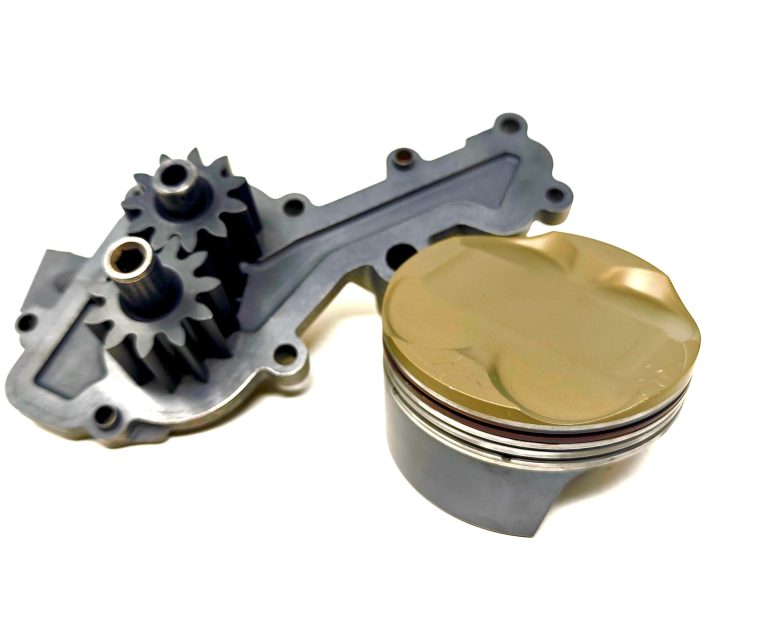
Beschichtete Motorteile eines Porsche 997 Saugmotors: Ölpumpendeckel mit Laufzeug und ein Mahle-Kolbens
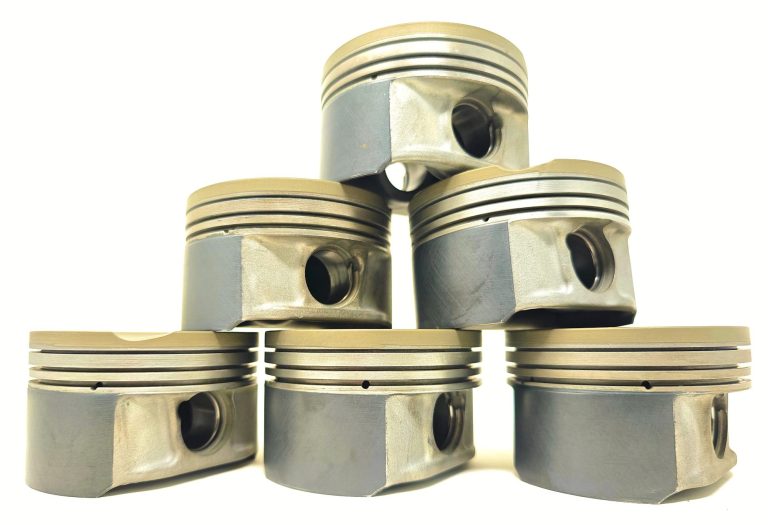
Foto von beschichteten Kolben eines 3,4 ltr. Motors.
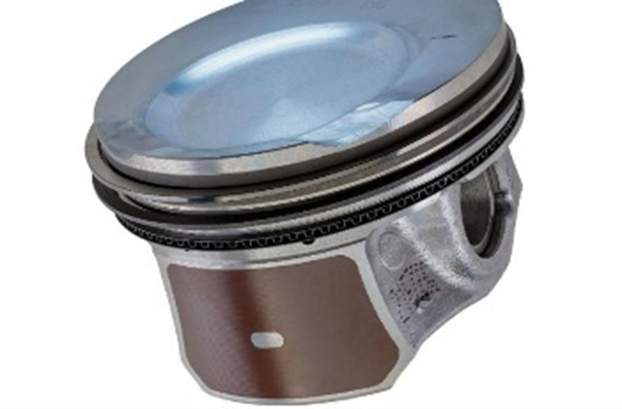
Foto 2: Das rostbraune ECO-TOUGH NG© Coating von Federal Mogul/Tenneco auf einem Kolben. Bildrechte: Federal-Mogul/Tenneco
Unser Kolbenmessprotokoll als Basis für alle Arbeiten
Neben dem Kolbenmessprotokoll, welches wir seitens der Ist-Werte erstellen, benötigen wir von Ihnen entsprechende Angaben über die Bohrungen der einzelnen Zylinder. Im Hinblick auf unsere spezielle Beschichtungstechnologie, müssen Sie umdenken, denn wir beschichten generell auf einen größeren Kolbenhemd-Durchmesser als es bei anderen Anbietern von Kolbenbeschichtungen üblich ist. Das Einbaumaß der von uns beschichteten Kolben liegt in der Regel zwischen 2 bis max. 3/100 mm
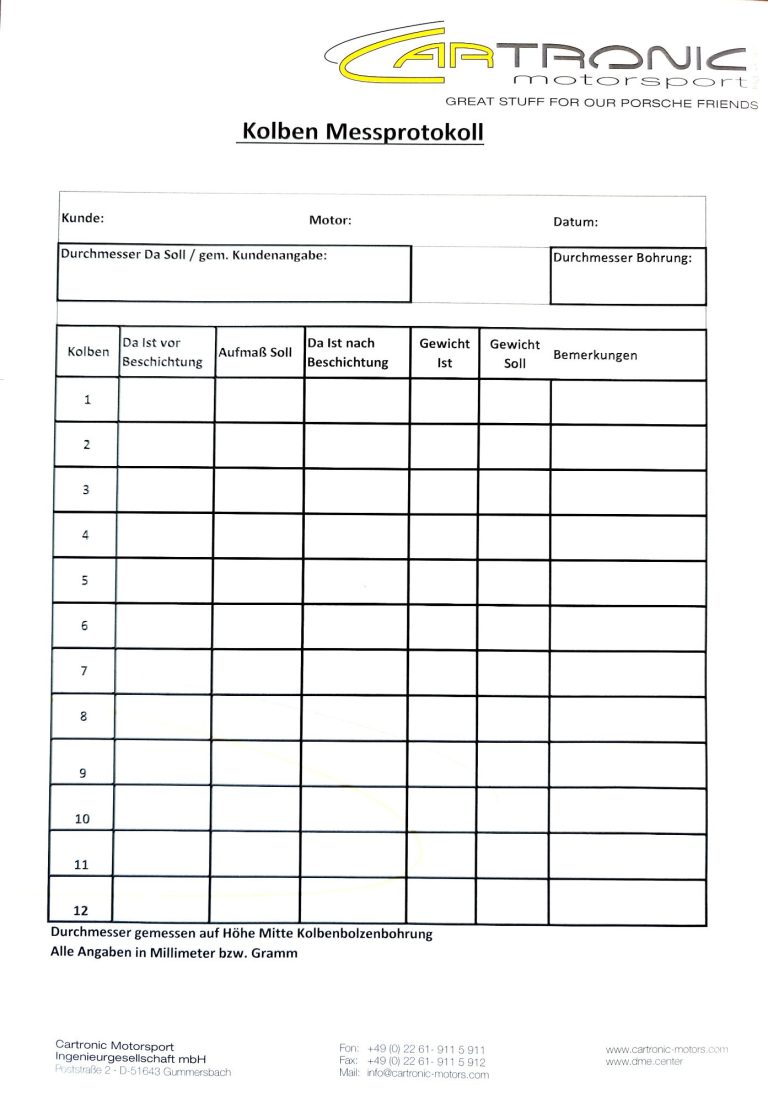
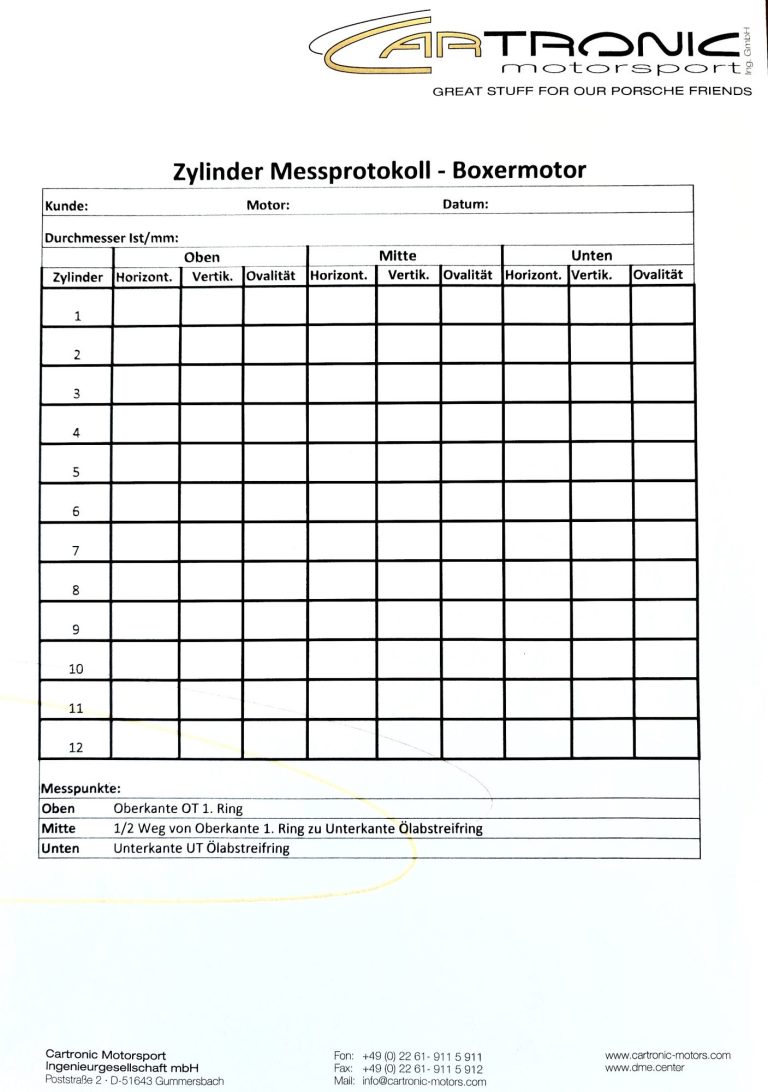
Das Zylindermessprotokoll
Um den "passenden" Kolbendurchmesser zu ermitteln macht es Sinn zu Beginn unserer Zusammenarbeit sich mit uns auszutauschen. Sie teilen uns Ihre Wünsche mit und wir passen diese ggfls. gemeinsam an. Generell gilt es ein enges Kolbenspiel zu erzeugen. Auch sprechen wir mit Ihnen über das Thema Kolbenring-Stoßspiel.
CPHC Cartronic-Piston-Heatschield-Coating
Das ultimative Hitzeschild für Kolbenböden und Brennraumkalotten
Beschreibung einer hochtemperaturresistenten Kolbenbodenbeschichtung zwecks Optimierung von gegenläufigen thermischen Expansionsverhältnissen von Kolben und Zylinder. Verringert das Risiko von Laufbahnschäden durch Kolbenklemmer und minimiert Verbrennungsrückstände am Feuersteg der Kolben. Steigert die Effizienz von Verbrennungsmotoren.
Moderne Motoren haben eng ausgelegte Laufspiele. Leider harmoniert die thermische Ausdehnung von Kolben nicht immer mit den Zylindern. Speziell nach dem Kaltstart und in der Warmlaufphase kann es zu Kolbenklemmern kommen. Um das Risiko zu minimieren, empfiehlt sich zusätzlich zur Kolbenhemdbeschichtung eine hochtemperaturbeständige keramische Beschichtung, die auf die Kolbenböden sowie den Feuersteg (Bereich oberhalb der Kolbenringnuten) aufgebracht wird. Bei der CPHC-Beschichtung handelt sich um ein nass aufgebrachtes und danach eingebranntes Dickschicht-Coating, welches dafür sorgt, dass die Verbrennungshitze zeitverzögert in den Kolben eingeleitet wird. Es handelt sich um eine sehr wirksame, thermische Barriere, welche bei evtl. auftretenden thermischen Spitzenbelastungen der Kolben vor einem Kolbenfresser bzw. Motorschaden schützt. Zudem verringert sich Temperatur im Bereich des Feuerstegs, was eine exzessive Verkokung des Kolbens oberhalb der Ringzone verhindert bzw. diese minimiert. Auch verbessert man dadurch die Wirkung der oberen beiden Kolbenringe, da mehr Brenngas in die Ringnut eindringen kann und langfristig die Anpressung der Kolbenringe an die Laufbahn bewirkt.
Unsere keramische Hochtemperatur-Beschichtungen, zeichnen sich durch eine unübertroffene Temperaturfestigkeit sowie eine hervorragender chemischer Beständigkeit gegen Kraftstoffe und bestimmte Radikale, die im Verbrennungsprozess gebildet werden aus. Die Beschichtungen basiert auf einer einzigartigen anorganischen Matrix. Die physikalische Stabilität darf man als ausgezeichnet bezeichnen.
Wir sprechen aus Erfahrung, denn ihre Wirksamkeit zeigte die Beschichtung bei von uns reparierten Porsche MA/1xx-Motoren mit Direkteinspritzung. Diese Motoren wurden der Nachfolger der M97/M97 Saugrohr-Einspritzern ab Modell 997/II und wurden ab Werk mit einem sehr geringen Kolbenspiel ausgeliefert. Zudem leiden sie an einen konstruktiven Mangel der nicht selten dazu führt, dass es bereits bei geringen Laufleistungen aufgrund von unterschiedlichen thermischen Ausdehnungsraten zwischen Kolben und den in den Block integrierten Alusil-Zylindern im unteren Totpunkt (UT) zu Kolbenfressern kommen kann. Die Zylinder dehnen sich dort auf Grund der massereichen Konstruktion weniger schnell aus als im oberen und mittleren Hubbereich in dem es deutlich weniger Blockmaterial (Aluminium) zu erwärmen gibt.
Selbstverständlich gibt es Lösungen für dieses Problem. Zum einen besteht die Möglichkeit die beschädigten Zylinder mit einer der beliebten Büchsen zu versehen. Bei Kolbenfressern, die nur zu einem sehr geringen Materialabtrag im Zylinder geführt haben, kann man das Problem mit Honen des oder der betroffenen Zylinder lösen. Technisch machbar ist eine Vergrößerung des Bohrungsdurchmesser um bis zu 12/100mm. Ohne eine nachfolgende Kolbenhemdbeschichtung ergäbe sich dann ein Kolbenspiel von zirka 15-16/100mm, was deutlich zu groß ist. Deshalb tragen wir eine entsprechend starke Kolbenbeschichtung aus. Das Ziel soll ein Kolbenspiel von 3/100mm, gemessen inkl. der Beschichtung sein. Final tragen wir dann noch unsere CHPC-Beschichtung auf den Kolbenboden auf. Das Risiko, dass es danach zu einem erneuten Kolbenklemmer kommt, wird dadurch deutlich minimiert.
In Kombination mit unserer Kolbenhemdbeschichtung, dem speziellen Laserhonverfahren, sowie dem Thermo-Coating, konnten wir in den letzten Jahren nahezu 50 Motoren erfolgreich reparieren. Die Beschichtung kann zwar nicht verhindern, dass es zu einem Wärmeeintrag in die Kolben kommt, jedoch verzögert sich die Auswirkung, was zu einer langsameren thermischen Ausdehnung des Kolbens führt. Grafisch ausgedrückt, erkennt man den Unterschied in der Zeitachse, die deutlich flacher verläuft, bis es irgendwann zu einem Temperaturausgleich kommt. Die thermische Ausdehnung der Kolben harmonierte dann mit der thermischen Ausdehnung der Zylinder. Die Beschichtung widersteht Temperaturen bis zu 1460°C aus. Ein weiterer Vorteil der Beschichtung ist die Steigerung der Motorleistung, weil weniger thermische Energie ungenutzt verloren geht. Das Thermo-Coating strahlt Hitze ab, was man messen kann, wenn man einen beschichteten Kolbenboden mit einem nicht beschichteten Kolbenboden mit einer offenen Gasflamme erhitzt. Außen, auf dem Kolbenboden misst man rund 25-28°C höhere Temperaturen bei beschichteten Kolben. Auf der Kolbenunterseite allerdings rund 15°C geringere Temperaturen.
Im Detail
Auf den Fotos sehen Sie Beispiele von Kolbenbodenbeschichtungen auf Porsche Kolben.
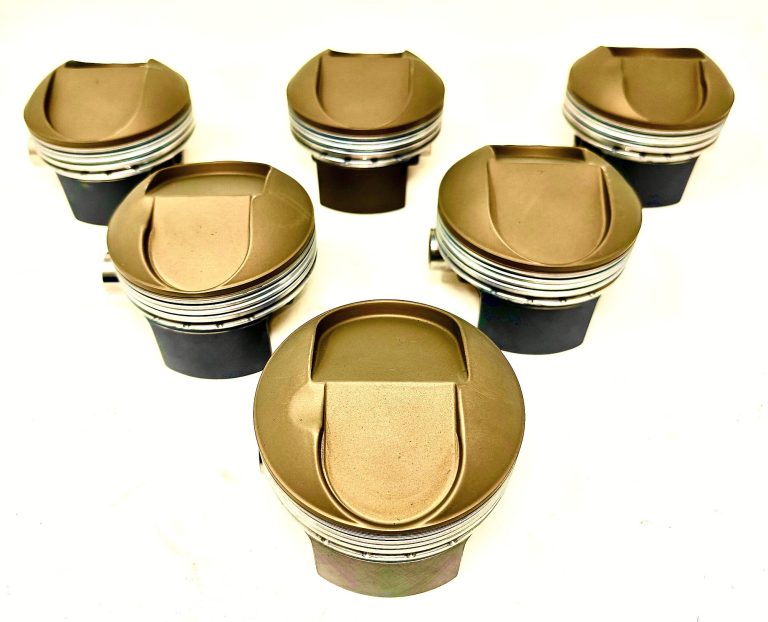
Kolben eines hochverdichteten Porsche 911 Rennmotors mit Kolbenhemd- und Kolbenbodenschichtung
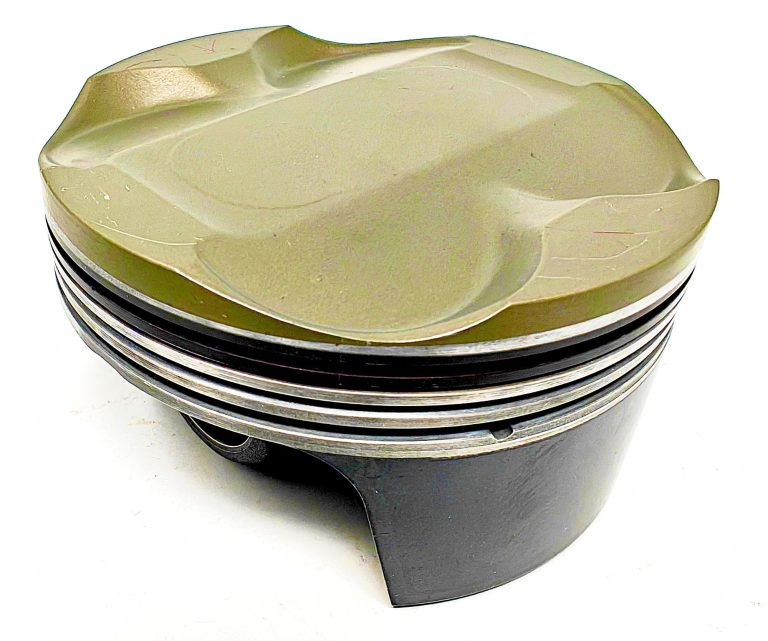
Kolben eines Porsche 997 Motors, Typ M97/01 mit Kolbenhemd-, und Kolbenbodenbeschichtung

Beschichteter Kolbenboden für einen 3,8L Porsche Motor
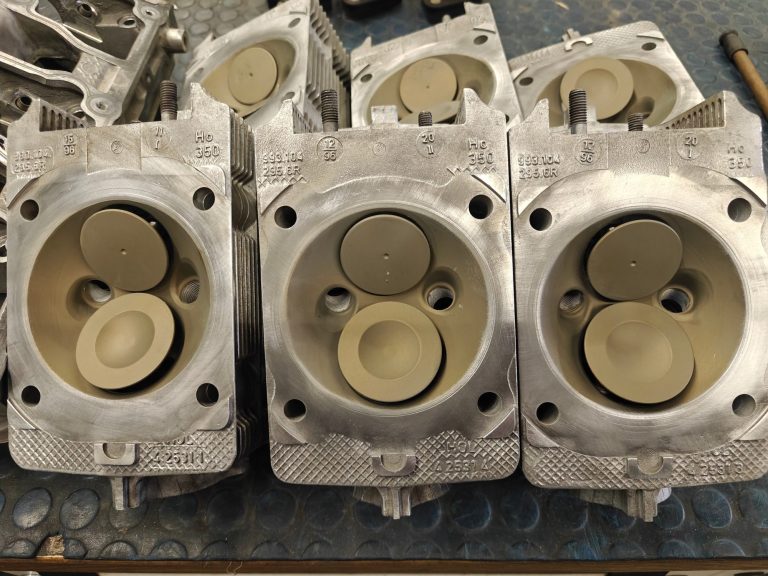
Brennraumkalotten und Ventile eines Porsche 993 Motors, versehen mit einem Thermo-Barrier-Coating zwecks Verlangsamung des Temperatureintrags in die Zylinderköpfe und Ventile. Diese Maßnahme verbessert den Verbrennungsablauf da hohe Materialtemperaturen verhindert werden, die zur unkontrollierten Zündung von Brenngasen führen kann. Speziell der innere Bereich des Übergangs von der Ventiltulpe zum Schaft wird durch das Cartronic CPHC-Coating geschützt.
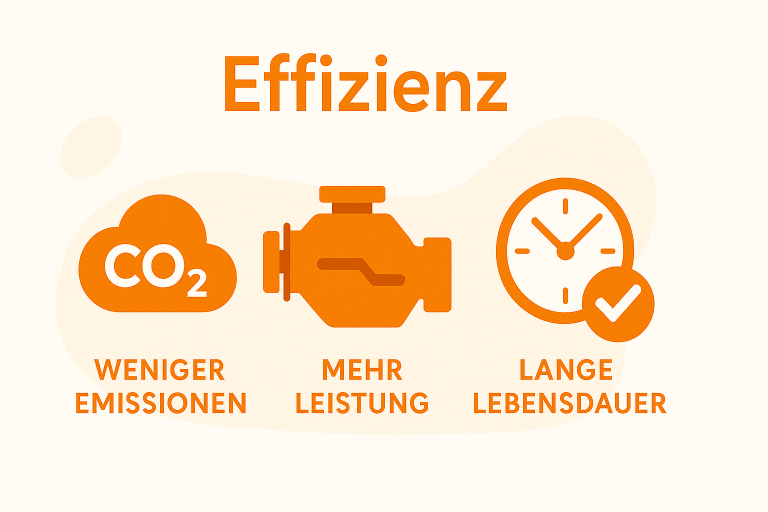
Effizienz, mehr Leistung und eine lange Lebensdauer
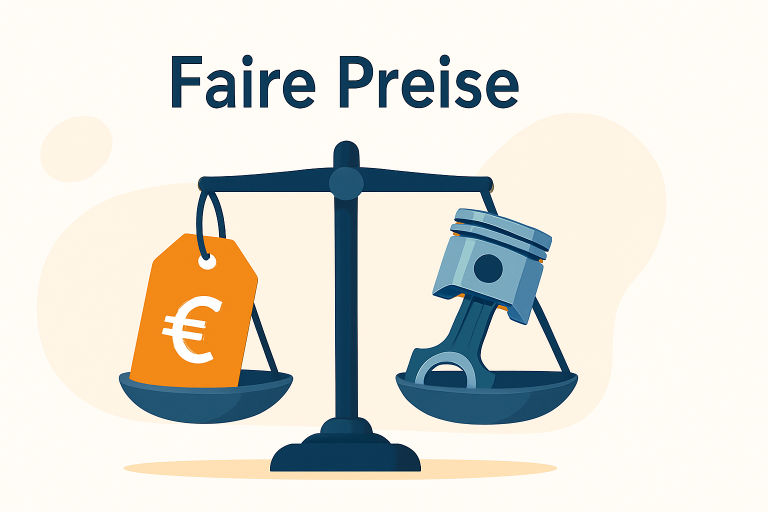
......zu fairen Preisen
CPLT Cartronic-Pistonskirt-Laserhoning-Technologie
Kolbenhemden mit gelaserter Kolbenhemdbeschichtung zwecks Optimierung der Öl-Rückhaltung
Beschreibung eines neuartigen Laser-Honverfahrens für Kolbenhemden zur Optimierung der Ölrückhaltefähigkeit zwecks Vermeidung von Kolbenfressern
Dass die Beschichtung von Kolbenhemden eine Herausforderung darstellt, erkennt man daran, dass fast alle herstellerseitig aufgebrachten Beschichtungen unzureichend haften und/oder recht schnell verschleißen. Da man uns im Tagesgeschäft regelmäßig mit schadhaften Kolbenhemdbeschichtungen von namhaften Kolbenhersteller konfrontierte, waren wir sicher, dass dies nicht den letzten Stand der Entwicklung darstellen konnte.
Aus diesem Grund entschlossen wir uns zu einer Eigenentwicklung. Nach über zwei Jahren Entwicklungszeit erreichten wir unser Ziel. Ende 2023 kam eine weltweit einzigartige, sich selbst adaptierende Kolbenhemdbeschichtung mit den weiter oben beschriebenen Eigenschaften auf den Markt.
Zu Beginn der Entwicklung wurde die Beschichtung nach dem Auftragen und der Einstellung der Schichtdicke abschließend und ausschließlich mit einem Kreuzschliff versehen. Das erfolgte händisch mit einem konventionellen 3M-Schleifpad. Dadurch verbesserten wir die Ölrückhaltung der Beschichtung. Da eine händische Bearbeitung in ihrer Qualität nicht reproduzierbar ist, suchten wir nach einer maschinellen Lösung. Leider führten die diversen Versuche mit unterschiedlichen Schleif-Technologien zu keinem befriedigenden Ergebnis. Eine gleichmäßige Bearbeitung der runden und zugleich balligen Flächen der Kolbenhemden schien unmöglich.
Im ersten Quartal des Jahres 2024 starteten wir eine Versuchsreihe mit einer bis dahin in diesem Bereich unbekannten Methode, die in recht kurzer Zeit zum gewünschten Erfolg führte. Wir waren sicher, dass man die Beschichtungsoberflächen unserer CTOAC-Beschichtung mit einem Laser derart bearbeiten kann, dass Ölrückhaltetaschen entstehen. Anzahl, Muster und Tiefe sollten einstellbar sein. Damit wären in der Lage, eine reproduzierbare und definierte Flächenstruktur herzustellen. Wir fragten bei einem bekannten Unternehmen an, welches industrielle Laseranlagen produzieren, ob Interesse an einer gemeinsamen Entwicklung einer Laser-Honanlage für Kolben besteht. Anfang des 3. Quartals 2024 wurden die Versuchsreihen erfolgreich abgeschlossen. Das Cartronic CPLT-Laserhonverfahren war geboren.
Spätestens im Herbst 2025 werden wir in der Lage sein, Beschichtungen von Kolbenhemden mit einer programmierbaren Laseranlage durchzuführen um damit mikroskopisch kleine Ölrückhaltetaschen in der Oberfläche der Beschichtung zu erzeugen. Dabei wird der zu bearbeitende Kolben in eine mikroprozessorgesteuerte Drehvorrichtung eingespannt. Die Intensität, die Frequenz als auch das Lasermuster den der auf den Kolben gerichteten Laserstrahl erzeugt, wird je nach Materialdicke und gewünschter Ölruckhaltung der Beschichtung eingestellt. Je nach gewählter Intensität entfernt der Laserstrahl nicht nur einen Teil das aufgebrachte Coating, sondern verdampft auch einen geringen Anteil des unter der Beschichtung befindlichen Kolbenmaterials (Aluminium). Die Haltbarkeit der Beschichtung, wurde nach ersten Befürchtungen nicht negativ beeinflusst, sondern sogar verbessert, denn wir stellten fest, dass im Randbereich der erzeugten Vertiefungen der Polyamidimid-Anteil der Beschichtung auf der rauen, gestrahlten Oberfläche der Kolbenhemden aufschmilzt und lokal eine sehr widerstandsfähige Haftung erzeugt.
Im Detail
Die beiden folgenden Abbildungen zeigen einen Kolben mit CTOC-Beschichtung auf dem Kolbenhemd, welche zwecks Optimierung der Ölrückhaltung einer speziellen Laserbehandlung unterzogen wurde. Die dritte Abbildung zeigt eine Mikroskopaufnahme der Beschichtung ohne Laserung.
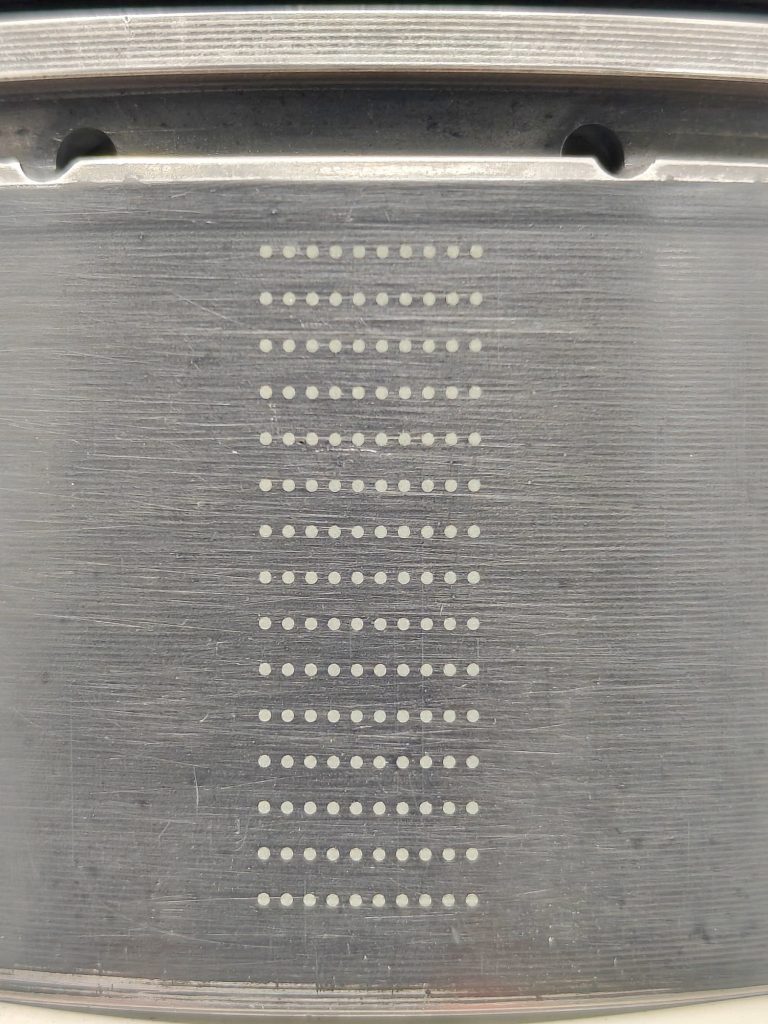
Kolbenhemd mit Laserung / Vergrößert
Schaut man sich die Verschleißmuster von Kolben an, erkennt man in welchen Bereichen es dem Kolben während des Motorlaufs "zu eng" geworden ist. Unsere Erfahrung hilft dabei, die Bereiche der Kolbenhemden einer Laserhonung zu unterziehen bei denen es Sinn macht.
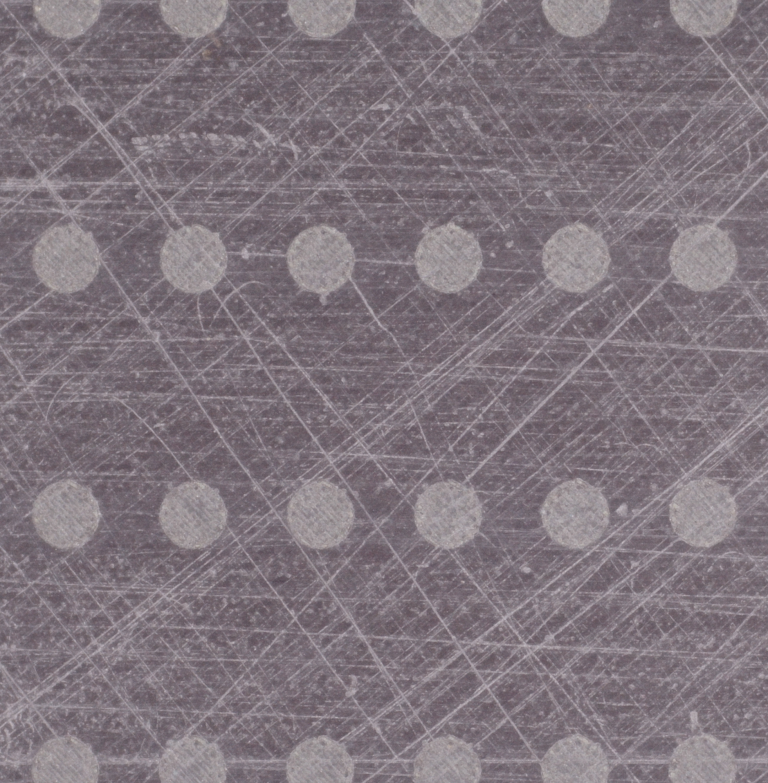
Laserung und Honmuster auf einem Kolbenhemd
Das Lasermuster wird je nach Anforderung ausgewählt. Sowohl die Tiefe als auch die Form (hier zirkular) und die Position auf dem Kolbenhemd gilt es auszuwählen.
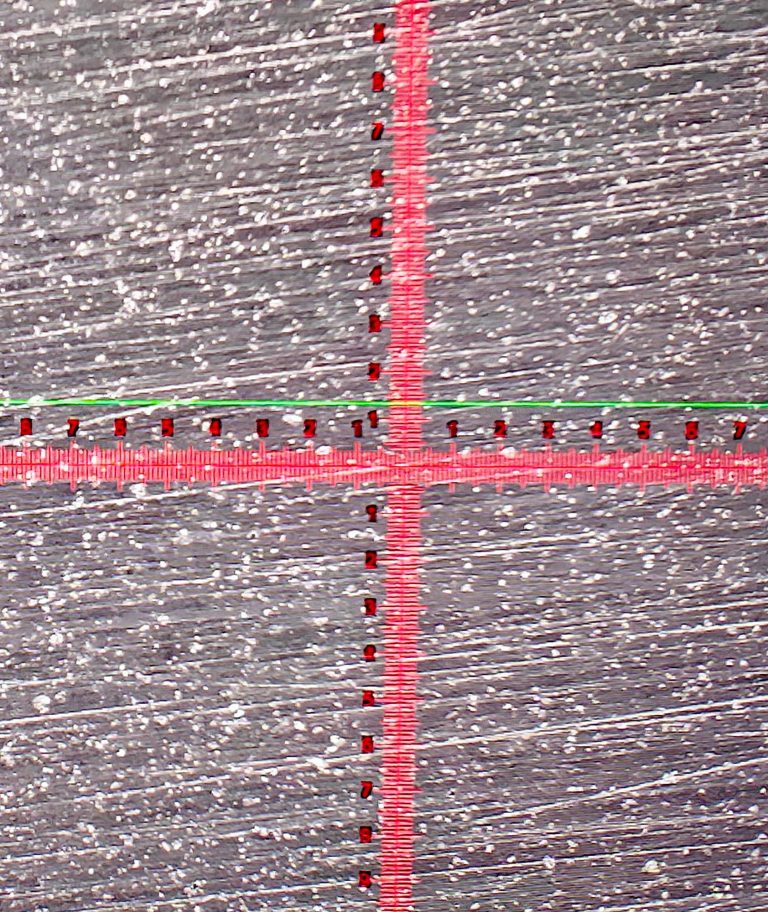
CTOC Beschichtung / 80fach vergrößert

Wie tief wird gelasert?
Hier erkennt man die Tiefe der Laserung. Die aufgetragene Beschichtung wird bis zu einer Tiefe von 5-8µm abgetragen. Die Bestandteile der Beschichtung schmilzt an diesen Stellen. Der Werkstoff verbindet sich mit dem darunterliegenden Aluminium und bildet eine sehr haltbare Öltasche in definierter Geometrie aus. Dieses Verfahren wurde von uns en twickelt und ist weltweit einzigartig.
CPIP Cartronic-Powder-Impact-Plating
CMST Cartronic-Micro-Shotpeening-Treatment
Zwei Verfahren zur Optimierung der Materialeigenschaften von Motorbauteilen durch moderne Strahlverfahren mit spährischem Mikro-Keramik-Strahlgut
Das CPIP Cartronic Powder-Impact-Plating Verfahren
Beschreibung eines neuartigen mechanischen Übertragungsverfahren von verschleißhemmenden Mikro-Partikeln in die Oberfläche von hochbelasteten Motorenbauteilen zwecks Verbesserung der tribologischen Eigenschaften, Erhöhung der Festigkeit sowie Verbesserung der Korrosionsverhaltens.
Je geringer die Reibung zwischen den Flächen der Kolbenringe und der Kolbenringnut ist umso besser funktionieren Kolbenringe und umso länger ist die Haltbarkeit von Kolben. Man muss wissen, dass nicht der optische Eindruck eines Kolbens darüber entscheidet, ob man einen gebrauchten Kolben weiterverwenden kann. Stellen Sie sich einen akribisch gereinigten Kolben vor, der mit einer Kolbenhemd und Kolbenbodenbeschichtung versehen wurde, aber über Ringnuten verfügt, die nicht mehr Maßhaltig sind. Dieser Kolben wäre, trotz einem hübsch aussehenden Äußeren, Schrott! An dieser Stelle stellen wir Ihnen ein von uns weiterentwickeltes, inernovatives Micro-Shotpeening-Verfahrens vor, welches es erlaubt Trockenschmierstoffen in die Oberfläche des Kolbenmaterials einzubetten. Festschmierstoffe, wie z.B. wie Zinn, Molybdändisulfid (MoS2) und einige andere an dieser Stelle nicht genannten High-Tech Materialien die an dem Keramik-Strahlmittel haften, werden während des Beschuss-Prozess in die Oberfläche des Kolbenwerkstoffs eingebettet. Dieser Prozess ist als PIP (Powder-Impact-Plating) bekannt. Damit erreicht man in einem Arbeitsgang neben der beschriebenen Verbesserung der Oberfläche durch Verdichtung und Glättung eine signifikante Verbesserung der tribologischen Eigenschaften.
Das ultrafeine Spezial-Strahlmedium das im Rahmen des Prozesses mit extrem hoher Geschwindigkeit auf die Oberfläche der Kolbennuten geschleudert wird, erzeugt an den unendlich vielen Auftreffpunkten der Mikro-Kugeln räumlich definierte Vertiefungen und generiert dabei eine flächige, homogene Verteilung bzw. Auflösung von Druckspannungen. Der Prozess erzeugt pro einzelnen Aufprall einer Keramikkugel auf die Oberfläche eine mikrothermische Reaktion (partielle Erhitzung) mit sehr geringer Eindringtiefe. Dadurch werden auch die immer feststellbaren Mikrorisse in der Oberfläche wirksam durch Verdichtung versiegelt und zugleich reibungsminimierende Stoffe in die Oberfläche des Grundmaterials eingelagert. Würden alle Kolbenringnuten während der Produktion diesem Prozess unterzogen, würde sich der Verschleiß der Ringnuten deutlich verringern.
Ringnuten sind recht schmal. Man benötigt also Strahlgut mit einem geringen Durchmesser. Diese Mikrokugeln, generieren Vertiefungen mit sehr geringen Radien und Eindringtiefen in der Oberfläche.
Diese Oberflächenoptimierung löst auf praktischem Weg auch das generelle Problem einer eventuell vorhandenen Materialversprödung (auch Wasserstoffversprödung genannt), die beim Härten von Metallen auftreten kann. Die zahlreichen Einschläge während des Prozesses erhöhen nicht nur die Druckeigenspannung, sondern bewirken auch, dass die messbaren Druckspitzen deutlich näher an der Oberfläche liegen. Shot-Peening in Verbindung mit dem Powder-Impact-Verfahren erzeugt ein Produkt, welches eine Oberflächenvergütung aufweist, die seines Gleichen sucht.
Auf Grund der Erzeugung von Mikrokratern und der Veredelung der Oberfläche durch die dadurch erfolgte Kompaktierung und dem zeitgleichen Einbringen von reibungsminimierenden Materialien in die Oberfläche, wird die Kontaktfläche zwischen den Flächen der Kolbenringnut und der Kolbenringe um zirka 30% reduziert. Behandelt man Kolbenringnuten mit diesem, unserem Verfahren, wird das Risiko einer Reibverschweißung, zwischen Kolbenring und Flächen der Kolbenringnut deutlich gesenkt. Die Kontaktflächen der Nuten zu den Kolbenringen werden durch dieses Verfahren tribologisch optimiert, da die Flächen nicht nur geglättet werden, sondern das gestrahlte Material des Kolbens partiell genau da verdichtet wird, wo es Sinn macht. Da während des Beschusses der Materialoberfläche Festschmierstoffpartikel eingelagert werden, stellt dieses Verfahren eine interessante Alternative für Kolbenhersteller dar, da man auf das Auftragen von Harteloxal im Bereich der Ringnuten verzichten kann.
Das Verfahren optimiert die Festigkeit und verlängert die Lebensdauer der behandelten Bauteile und damit des gesamten Triebwerks.
Das CMST Cartronic-Micro-Shotpeening-Treatment
Beschreibung eines Kugelstrahlverfahrens mit Micro-Keramik-Strahlgut zwecks Optimierung der Festigkeit von hochbelasteten Motorbauteilen
Dabei handelt es sich um ein bei uns in der Entwicklung befindliches Mikro-Kugelstrahlverfahren von stark beanspruchten Motorteilen. Diese Oberflächenbehandlung sorgt dafür, dass feinste oberflächige mechanische Bearbeitungsspuren durch den Aufprall von ultrafeinen Micro-Keramikkugeln geglättet werden. Dadurch werden auch Spannungen im Material entfernt. Es entstehe eine definiert unregelmäßige Oberfläche mit unzähligen, mikroskopisch kleinen, halbkugeligen Vertiefungen (Kalotten genannt) ähnlich einer Golfballoberfläche. Diese Oberflächenbeschaffenheit ist auch in der Lage, bei gewissen Bauteilen (Kolben/Zylinder) von Verbrennungsmotoren Öl zurückzuhalten. Die grafischen Darstellungen "Micro-Shotpeening-Treatment" in Abb. 11 zeigen verschiedene Oberflächenstrukturen, die durch Sandstrahlen (links), konventionelles Kugelstrahlen (Mitte) und durch unser Mikro-Keramikkugelstrahlen (rechts), entstanden sind und verdeutlicht die Unterschiede der Behandlungen.
Es handelt sich um ein Kaltbearbeitungsverfahren, bei dem die Werkstückoberfläche mit kleinen kugelförmigen Strahlmitteln aus Stahl bzw. Keramik verfestigt wird. Jede Kugel, die auf die Oberfläche des Werkstücks trifft, wirkt dabei wie ein winziger Schmiedehammer, der eine flache Kalotte hinterlässt. Dabei wird die Metalloberflächenschicht gedehnt, also verformt. Tiefer unter der Oberfläche liegende Materialschichten wirken gegen diese Verformung und „versuchen“ die Oberfläche wieder in den Ursprungszustand zurückzubringen, was nicht möglich ist. Warum sich dieses Verfahren positiv auf Materialeigenschaften des Werkstücks auswirkt, erklärt sich aus der Tatsache, dass dabei im Bereich unter der Kalotte ein Bereich durch den Beschuss mit dem Strahlgut erzeugt wird, der über eine hohe Druckeigenspannung verfügt. Gestrahlt wird mit einem recht hohen Druck in vorher definierten Auftreffwinkeln und mit Strahlgut mit sehr geringen Durchmessern. In der Realität werden dabei sich überlappende Kalotten erzeugt, ähnlich wie eine Orangenhaut. Diese generieren eine gleichmäßig hohe Druckeigenspannung in den Bauteilrandzonen nahe der Oberfläche. Man strebt mit diesen Verfahren eine homogene und möglichst tiefe Spannungsverteilung unter der Bauteiloberfläche an.
Ein Blick in die Zukunft - Das Laser-Peening-Verfahren
Alternativ zu den Kugelstrahl-Verfahren werden auch sogenannte Laser-Peening-Verfahren angewendet. Bei diesem Verfahren wird die Bauteiloberfläche mit einem Hochleistungs-Laser beschossen. Das Bauteil selbst wird dabei durch eine klare Schutzschicht (meist Wasser) vor einem Volumenverlust geschützt. Da kein physisches und abrasives Strahlmittel eingesetzt wird, kann es zu keiner Kontamination kommen. Die dabei erreichbare Oberflächenstruktur ist ausgezeichnet. Wie kann ein Laserbeschuß zu einer Materialverformung führen. Das Laser-Peening beruht auf Schockwellen die auf das Bauteil auftreffen um die gewünschten Druckeigenspannungen zu erzeugen. Mit diesem Verfahren kann man verhältnismäßig tiefe Druckeigenspannungsschicht bei minimaler Kaltverfestigung der Randzonen erreichen. So können Druckspannungen in Schichten von bis zu 1,5 mm Tiefe bei Einsatzstählen und von 3,5 mm bei Aluminiumlegierungen erzielt werden. Durch herkömmliches, mechanisches Kugelstrahlen werden mit Keramikkugeln maximal zwischen 0,10-0,15mm und mit Stahlkugeln (auf Grund des höheren Gewichts) rund 0,20mm Tiefe erreicht. Auch ist die Druckspannungsverteilung unregelmäßiger.
Im Gegensatz zum Kugelstrahlen (Orangenhaut) hinterlässt das Laserstrahlverfestigungsverfahren eine deutlich glattere Oberfläche. Dies ist besonders vorteilhaft bei Anwendungen, die sowohl eine verbesserte Spannung als auch eine bessere Oberflächenqualität erfordern, wie z.B. bei Turbinenschaufeln in der Luft- und Raumfahrt und auch bei Kolben von Verbrennungsmotoren. Durch die nur sehr gering von der originalen Oberflächenrauheit abweichende Qualität können kostspielige und zeitintensive Nachbearbeitungsschritte entfallen.
Einen weiterer Vorteil sieht man darin, dass der Abbau der durch einen Beschuss mit einem Laser erzeugten Druckeigenspannung durch Temperatureinfluss bei Superlegierungen, wie z.B. bei Titan oder Inconel usw., wesentlich geringer ist als bei der durch mechanisches Kugelstrahlen erzeugten Druckeigenspannung. (siehe grafische Darstellung am Ende des Text)
Cartronic beschäftigt sich zur Zeit intensiv mit diesem Verfahren. Speziell bei geometrisch engen Bereichen, wie Kolbenringnuten die für mechanische Verdichtungsverfahren nicht gut erreichbar sind, kann eine räumlich definierte Bearbeitungsfläche sinnvoll sein.
Laser-Peening wird zunehmend für kritische Motorenteile wie Kolben und Kurbelwellen eingesetzt. Die Verbesserung der Ermüdungslebensdauer in hochbelasteten Bereichen beträgt beim Laserstrahlen in der Regel mehr als 50 %. Dies ist besonders wichtig für Bauteile, die extremen thermischen und mechanischen Bedingungen (Schwingungen / Druck usw.) wie z.B. Kolben oder Turbinenteilen, ausgesetzt sind. Obwohl das Laserstrahlen teurer als alle anderen Peening-Verfahren ist, sind die Vorteile in Bezug auf Endlebensdauer der behandelten Bauteile und Leistung erheblich, so dass es sich ideal für Anwendungen von Komponenten in Hochleistungsfahrzeugen eignet.
Im Vergleich zu den unterschiedlichen, konventionellen Schleif/Honprozessen mit gewünschter Rautiefe, würde sich bei einer Zylinderoberfläche, die man mit Mikro-Keramikkugeln oder mit einem Laser behandelt hätte, wesentlich weniger initialer Verschleiß zwischen den Reibpartner zeigen. Zudem würde man damit die Ölrückhaltung, als auch die Ölabstreifung durch die Kolbenringe verbessern. Da die Rautiefe zudem deutlich geringer ist als die bei konventionell gehonten, bewusst riefigen hergestellten Oberflächen, unterliegen die Kolbenringe deutlich weniger Verschleiß. Zur Zeit umgehen wir den initialen Verschleiß durch unser im weiteren Verlauf beschriebene, händisch durchgeführtes vertikales CVFH Fein-Honverfahren.
Die Grafik "Die Wissenschaft der Ölrückhaltung" am Ende des Textes verdeutlicht grafisch den Unterschied zwischen einer auf Hochglanz polierten Reibfläche (links) und eine Fläche die mit unserem Spezialstrahlverfahrens behandelt wurde (rechts). Zum besseren Verständnis: Je glatter die Oberfläche (Reibfläche) umso geringer die Ölrückhaltung. Die Kunst liegt darin, möglichst glatte, also reibungsarme Flächen zu erzeugen, die aber trotzdem über ein definiertes Ölrückhaltevermögen verfügen. Sicher ist, dass die Herstellung einer definierten Oberfläche durch dieses Verfahren, speziell bei Zylinderlaufbahnen erhebliche Vorteile zu den bis heute angewendeten Honverfahren zeigen werden. Die ersten Versuchsergebnisse mit dem Cartronic Verfahren behandelten Nikasil,- und Graugusszylindern sind vielsprechend. Sobald das Verfahren serienreif ist, erfahren Sie mehr.
Im Detail
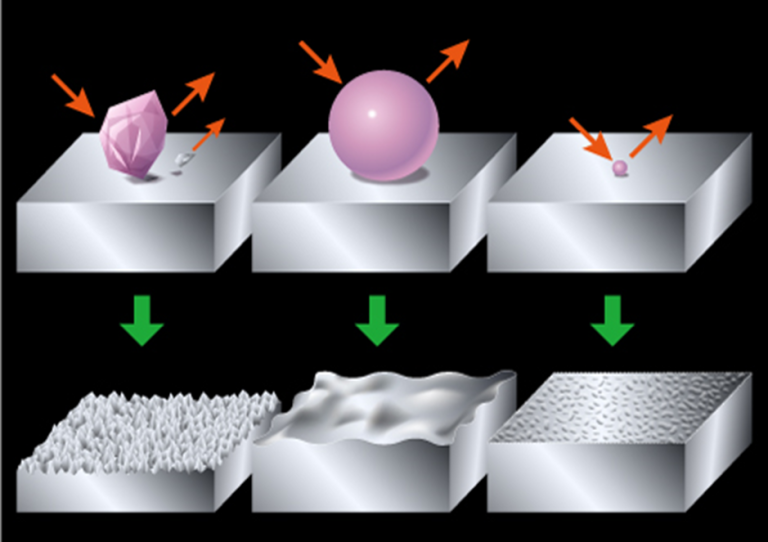
Micro-Shotpeening-Treatment
Abb. 11: Grafische Darstellung einer Oberfläche nach sandstrahlen (links), nach konventionellen Kugelstrahlen (mittig) und dem Cartronic CMST-Verfahren (rechts).
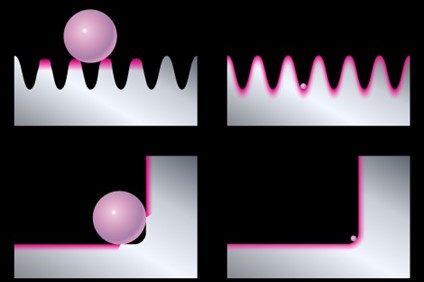
Kugelstrahlverfahren vs. Mikro-Kugelstrahlverfahren
Zeigt die Vorteile des Cartronic-Verfahrens mit Mikro Keramik-Kugeln (rechts) im Vergleich zu dem herkömmlichen Kugelstrahlverfahrens (links)
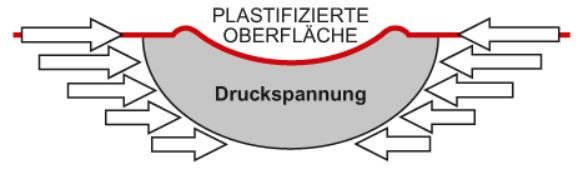
Ideale Druckspannungsverteilung nach dem Shotpeening-Prozess
Grafische Darstellung der Druckspannungsverteilung unter einer durch den Aufprall einer Keramikkugel entstandenen Kalotte. Bildrechte / Quelle: MIC. LLC
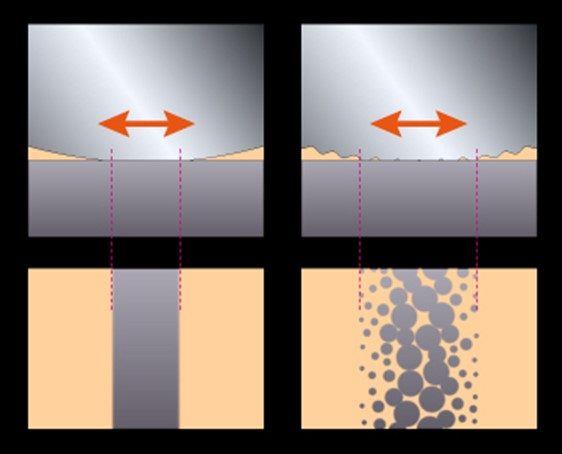
Die Wissenschaft der Ölrückhaltung
Grafische Darstellung: Vergleich der Ölrückhaltebereiche einer glatten, polierten (links) und einer durch das CMCS-Verfahren mikrogestrahlten Oberfläche (rechts). Die Herausforderung besteht darin, möglichst glatte, also reibungsarme Flächen zu erzeugen, die aber trotzdem über ein definiertes Ölrückhaltevermögen verfügen
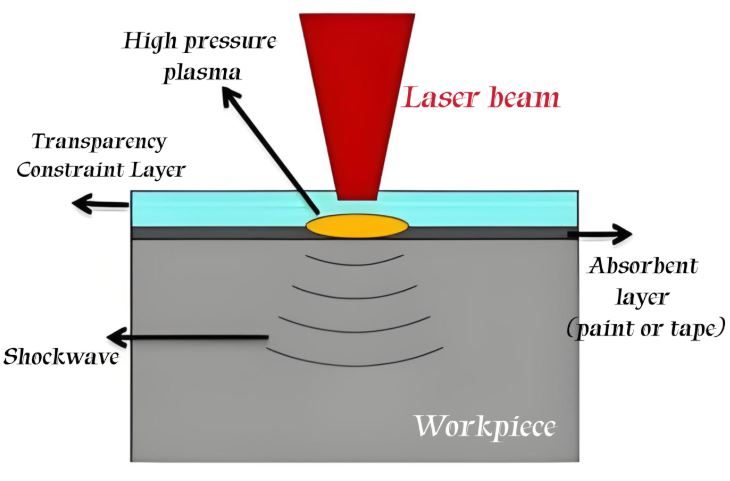
Laser-Peening
Grafik: Schematische Darstellung des Laser-Peening Verfahrens
Die Entwicklung schreitet mit großen Schritten voran. Einiges spricht dafür, dass es sich bei diesem Verfahren um die Technologie der Zukunft handelt.
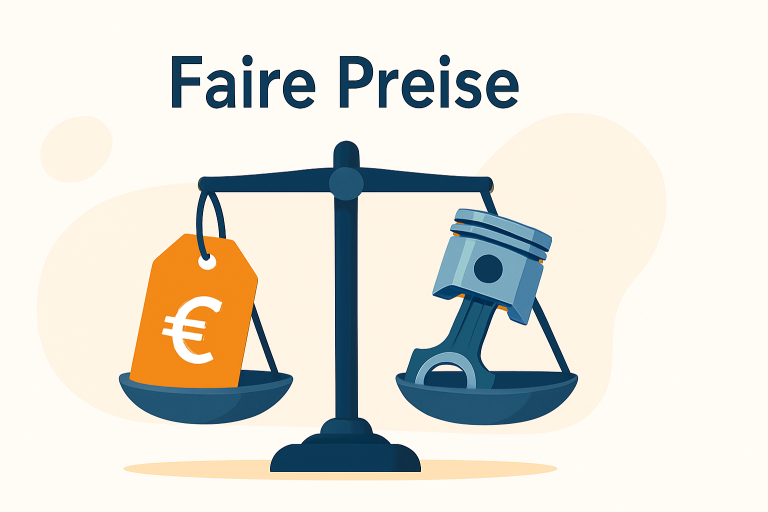
Faire Preise
Transparente Preise sind die Grundlage für eine vertrauensvolle Zusammenarbeit. Deshalb gestalten wir unsere Preise nachvollziehbar und fair. Uns ist wichtig, dass auch unsere Lieferanten für ihre Arbeit angemessen bezahlt werden!
CVFH Cartronic-Vertical-Fine-Honing
Optimierung der Zylinderlaufflächen und der Kolbenringe
Beschreibung eines neuartigen Honverfahrens zwecks Optimierung der Zylinderlaufflächen
Der von Cartronic perfektionierte vertikale Feinhon-Prozess stellt den letzten Schritt der Bearbeitung einer Zylinderlaufbahn dar und kann bei jeder Oberfläche (Grauguss, Schleuderguss, Nikasil (Mahle-Prozess), Alusil (KS-Produkt), Plasmaspritzflächen und anderen angewendet werden. Diese Feinbearbeitung kappt die Spitzen der beim Honen entstanden „Berge“. Auch wenn diese bereits durch ein spezielles Plateauhon-Verfahren zu „Tafelbergen“ verändert wurden, bewirkt diese Art der Bearbeitung eine zusätzliche Abrundung der Plateaus, also den Bereich am Rande des „Abgrunds“. Bildlich lässt sich die Auswirkung und das Ergebnis dieses Verfahrens auch darstellen. Die Grafik weiter unten ist leicht verständlich. Wichtig bei dieser Art der Oberflächenglättung ist die Richtung der Bewegung. Es muss zwingend vertikal in der Richtung gehont werden, in der sich der Kolben bewegt. Je nach Hub (Kurzhuber / Langhuber) verwendet man unterschiedliche Honwinkel. Nehmen wir an, der Zylinder wäre mit einem Honwinkel von 45° bearbeitet worden. 45° bedeutet, dass der Kolben die entstanden Riefen mit einem 45° Winkel passiert. Die zu Beginn der Einlaufphase scharfen Kanten der Kolbenringe „rasieren“ dabei förmlich die Spitzen der „Berge“ ab. Das erzeugt nicht nur mikroskopisch kleine Metallpartikel, die in das Motoröl eingetragen werden, in die Oberflächen von Pleuel- und Kurbelwellenlager eindringen und auch in fast allen Fällen sehr feine Kratzspuren auf der Oberfläche der Kolbenhemden und der Kolbenringe. Sich dabei ablösende Mikro-Partikel erzeugen die sehr feinen transversal verlaufenden Kratzer in der Oberfläche der Zylinderlaufbahn. Das sind alles unerwünschte Effekte, die es zu vermeiden gilt und man vermeiden kann.
Man sagt, dass die Einlaufphase der Kolbenringe zu den Zylindern eines Motors nach spätestens 2000 Km abgeschlossen ist. Verwendet man in den ersten 500 Km mineralisches Einlauföl, verringert sich die Einlaufzeit auf rund 1000-1200km. Die Phase startet mit einem verhältnismäßig hohem Verschleiß in den ersten 100 Km und reduziert sich im Laufe der Zeit immer mehr um irgendwann gegen Null zu tendieren. Hier geht es um eine manuelle Methode, mit der man nicht nur die Einlaufphase um rund 80% verkürzen kann, sondern auch deutlich weniger unerwünschte Metallpartikel in das Motoröl einträgt. Ölanalysen beweisen, dass sich dadurch den in dieser Zeit generierten metallischen Abrieb um zirka 90% verringert. Unsere Methode ist in der Branche noch weitestgehend unbekannt. Die Vorgehensweise ist unkompliziert und sehr einfach in der Durchführung. Bitte vertrauen Sie weiter in die moderne Hontechnik die mit teilweise sündhaft teuren Maschinen und Spezial-Honleisten durchgeführt wird, denn ohne diese geht gar nichts. Halten wir aber an dieser Stelle fest, dass gute klassische Handarbeit auch im High-Tech Zeitalter nicht wegzudenken ist, weil sie die maschinellen Ergebnisse deutlich verbessert.
Was können wir nun für Sie tun bzw. nicht tun?
Leider können wir Ihnen nicht die Zylinder in den Motoren honen an denen Sie arbeiten, außer Sie senden uns einzelne Zylinder von luftgekühlten Motoren zu. In Frage kämen Zylinder von Porsche 911 Motoren, von Motorrädern oder sonstige luftgekühlte Einzelzylindern. Auch nasse Büchsen können wir für Sie honen. Aber macht das Sinn?
Sie sollten sich unsere, im eigenen Haus produzierten, Honwerkzeuge kaufen. Diese gibt es passend für die unterschiedlichen Bohrungsdurchmesser.
Teilen Sie uns einfach den Bohrungsdurchmesser mit den Sie bearbeiten möchten und wir stellen Ihnen kurzfristig den dafür passenden Hand-Honzylinder zu einem sehr fairen Preis her. Dieser wird von uns direkt mit den entsprechenden Streifen der Schleif-Pads ausgeliefert.
Die Schleifpads gibt es in drei unterschiedlichen Körnungen (fein/mittel/grob) und werden aufgeklebt. Ersatzstreifen können Sie jederzeit nachbestellen. Der Basiskit besteht aus einem Honzylinder mit Handgriff sowie jeweils 2 Schleifstreifen der Körnung Grob und Mittel und 3 Streifen der Körnung Fein.
Tipp: Optimale Ergebnisse erzielt man, wenn man sich zirka 10 Minuten mit jedem Zylinder beschäftigen. Der letzte Arbeitsgang erfolgt immer mit der feinsten Körnung und sollte zirka 5 Minuten andauern. Minimale Benetzung der Zylinderoberfläche mit einem feinen Sprühöl kann nicht schaden.
Um wirklich alles getan zu haben, empfehlen wir Ihnen zusätzlich zum Fein-Honen der Laufbahn noch eine Feinpolitur der Kolbenringflanken. Herstellerseitig aufgebrachte Farbmarkierungen auf den Ringen sollten vor Montage und Inbetriebnahme des Motors entfernt werden, da sich diese nach dem erfolgten Vertikal-Honprozess erst nach recht langer Zeit abtragen und generell „verdächtige“ dunkle Streifen in der Zylinderlaufbahn hinterlassen. Das führt ständig zu Verwirrungen bei durchgeführten Endoskopien von Brennräumen und Zylinderlaufflächen. Dass dafür benötigte Material liefern wir Ihnen gleich mit.
Die Ergebnisse sind umwerfend. Sie werden überrascht sein.
Im Detail
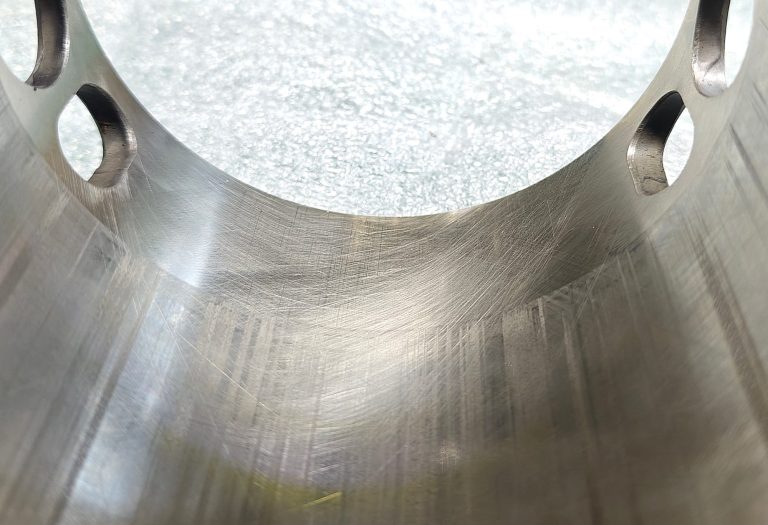
Zylinderlaufbahn mit vertikalen verlaufenden Riefen auf Grund von mangelhaften Federn von MAHLE-Ölabstreifringen für Porsche 997 M97/01 Motoren. Die Oberfläche wurde nicht vertikal gehont und erscheint matt-glänzend, champagnerfarben.
Diese beschädigte mit nicht normativen Riefen versehene Zylinderoberfläche entstand in Folge des Einbaus neuer MAHLE Aftermarktkolben die seitens des Herstellers mit falschen Federn im Ölabstreifring-Paket ausgeliefert wurden. MAHLE als potenziell "unfehlbare" Weltfirma lehnte jegliche Gewährleistung ab. Wir befinden uns kurz vor der Eröffnung eines Gerichtsverfahrens welches unsere Handel-Handwerk-Versicherung initiieren wird. Die oben sichtbare Oberfläche wurde nicht bearbeitet. Bitte vergleichen Sie das Erscheinungsbild zu der Oberfläche eines von uns vertikal gehonten Zylinders aus dem selben Motor rechts.
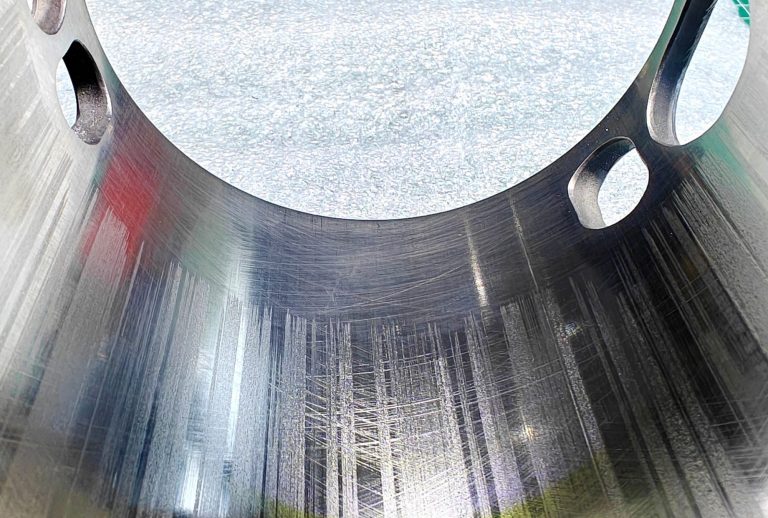
Zylinderlaufbahn mit vertikalen Riefen die von mangelhaften MAHLE-Ölabstreifringfedern erzeugt wurden, zeitweise montiert in Kolben für Porsche 997 M97/01, 3,8ltr. Motoren. Die Oberfläche wurde von uns zur Verdeutlichung der Wirkung des Vertikal-Honing händisch für zirka 10 Minuten gehont und erscheint hochglänzend, neusilberfarben.
Das Foto zeigt die bearbeitete Oberfläche der beschädigten und nicht vertikal gehonten Zylinderlaufbahn auf dem linken Foto. Diese wurde von uns im Rahmen von Versuchen in Handarbeit innerhalb von 10 Minuten vertikal gehont. Das Cartronic-CVFH Verfahren führt innerhalb einer kurzen Bearbeitungszeit zu unglaublichen Ergebnissen. Die Oberflächen-Rauhigkeit der Zylinderlaufbahn verringert sich deutlich, da alle "Berg-Spitzen" in der Honfläche gekappt, bzw. abgerundet werden. Das Honverfahren darf zwingend nur in vertikaler Richtung (Laufrichtung des Kolbens) erfolgen.
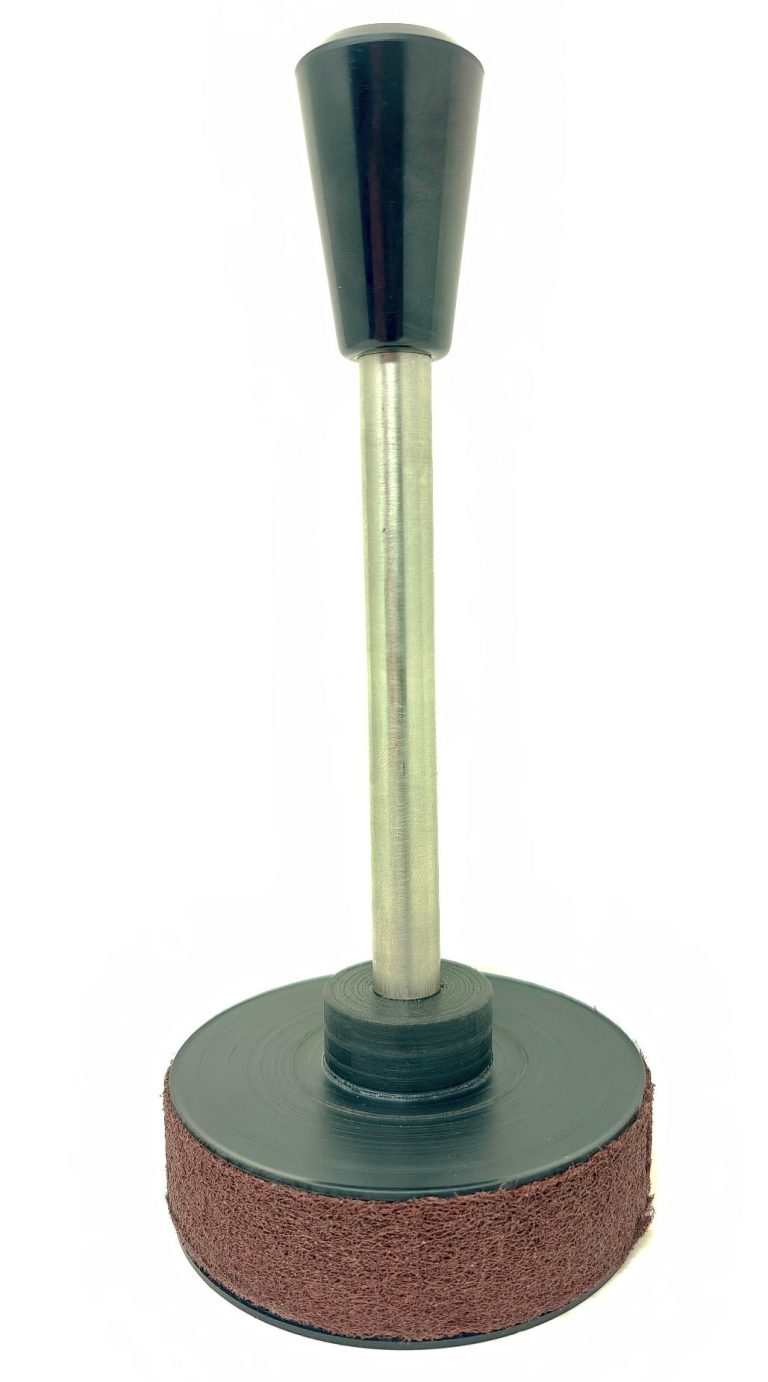
Das konstruktiv einfache, aber geniale Vertikal-Honwerkzeug
Das abgebildete Honwerkzeug wurde von uns entwickelt und wird mit 3M-Schleifpads verschiedener Körnungen bestückt. Bei Interesse an diesem einfach genialen Werkzeugs, kontaktieren Sie uns bitte per Mail. Wir benötigen nur den zu bearbeitenden Bohrungsdurchmesser. Copyright: Cartronic
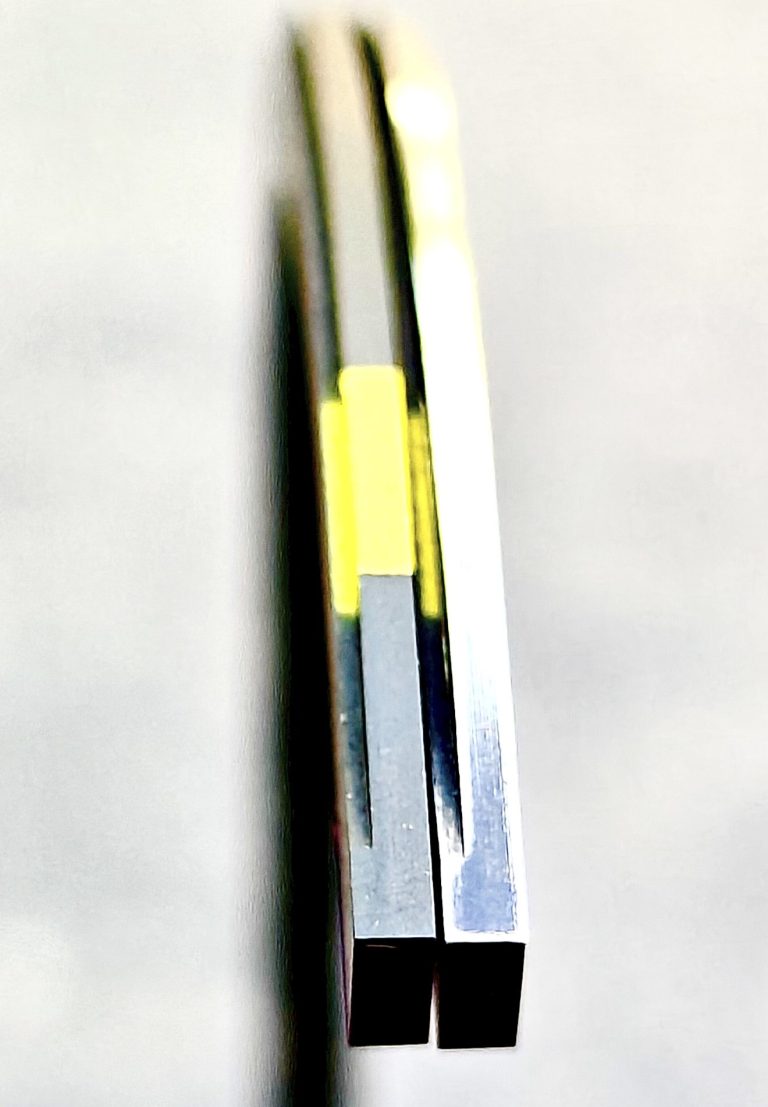
Vergleich von unbearbeiteten und optimierten Kolbenringen
Links: Unbearbeiter, einbaufertiger Nasen-Minutenring, passend für einen M97/01 Porsche Motor mit Mahle-Kolben. Rechts, der gleiche Ringe aber mit entfernter Farbmarkierung von der Ringflanke und Feinschliff der Flächen und Kanten mit 7000er Körnung. Empfehlenswert in Kombination mit vertikal gehonten Zylinderflächen. Die Einlaufphase verkürzt sich durch diese Maßnahmen erheblich. Copyright: Cartronic
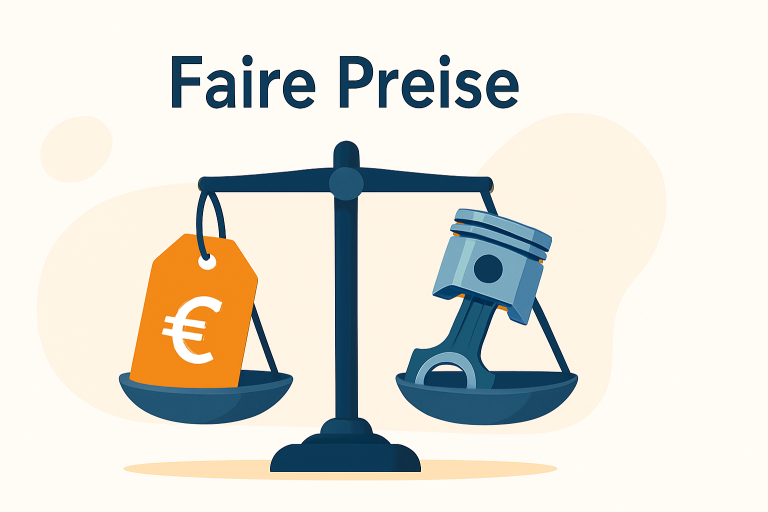
Faire Preise
Transparente Preise sind die Grundlage für eine vertrauensvolle Zusammenarbeit. Deshalb gestalten wir unsere Preise nachvollziehbar und fair. Uns ist wichtig, dass Sie, als unser Kunde, Vorteile aus der Zusammenarbeit ziehen können.
Honwerkzeug als Set für Bohrungen:
70-80mm € 258,--
81-90mm € 278,--
91-99mm € 298,--
Lieferumfang: Honwerkzeug mit Handgriff für gewünschten Bohrungsdurchmesser inkl. 2 Schleifpad-Streifen Körnung Grob, 2 Schleifpad-Streifen Körnung Mittel, und 3 Schleifpadstreifen Fein. Bitte den genauen Bohrungsdurchmesser angeben!
alle Preise inkl. 19% Mwst.
Besuchen Sie uns im Gummersbach
Wir freuen uns auf Ihre Kontaktaufnahme. Vereinbaren Sie doch einfach einen Termin für ein Beratungsgespräche bei uns im Hause.